The Urethane Blog
Everchem Updates
VOLUME XXI
September 14, 2023
Everchem’s exclusive Closers Only Club is reserved for only the highest caliber brass-baller salesmen in the chemical industry. Watch the hype video and be introduced to the top of the league: — read more
December 6, 2023
Brenntag reshuffles business amid calls for full break-up
By Tristan Veyet and Matteo Allievi
December 5, 20237:40 AM ESTUpdated 2 days ago
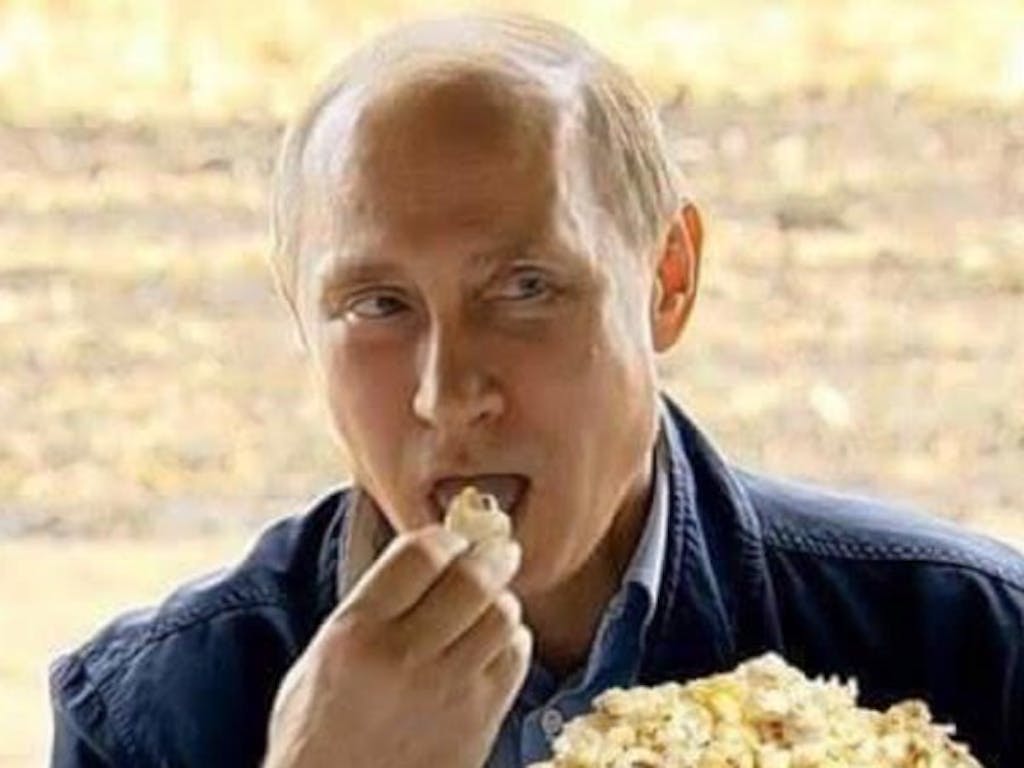
Dec 5 (Reuters) – German chemicals distributor Brenntag (BNRGn.DE) said on Tuesday it would reorganise its business into two independent divisions from 2024 as it faces pressure from activist investors to break up the company.
The group’s shares were down 1.6% at 1012 GMT. Analysts had expected a muted share price reaction after no clear split was announced.
In the reshuffle, Brenntag’s essentials unit, a wholesale business for process chemicals, and the specialties arm, which provides services to industries such as nutrition and household products, will each have their own legal structure and leadership.
Brenntag said ahead of its Capital Markets Day event that the structural changes would give the company more options and make it ready for the next strategic steps by 2026, but did not specify what those steps might be.
“Split between two divisions is one option but there could be also other options,” CEO Christian Kohlpaintner said during a press conference.
Brenntag’s management has faced increasing pressure for a break-up of its businesses and a spin-off of the specialties unit from activist investors who have argued the separation would boost the company’s shares.
“There is really no catalyst to buy the shares unless Brenntag announces a clear split of the two divisions before 2026,” Alster analyst Thomas Wissler said.
Brenntag is the latest in a series of old and famous German companies, such as Bayer (BAYGn.DE) and Thyssenkrupp (TKAG.DE), that have been targeted by activist investors to divest part of their business to improve profitability.
As part of the reorganisation, Brenntag will transfer all pharmaceutical activities from the essentials arm to the specialties unit, while moving water treatment and finished lubricants businesses along with some semi-speciality products in the opposite direction.
As a result, the specialties division will account for 30% of the group’s gross profits, while essentials will make up the rest.
Brenntag said it aimed to grow its organic earnings before interests, taxes and amortisation by 7-9% per year until 2027, with 5-7% growth in essentials and 7-9% growth in specialties.
($1 = 0.9240 euros)
(This story has been corrected to attribute descriptions of divisions to correct business units, in paragraph 3)
Reporting by Tristan Veyet and Matteo Allievi in Gdansk; editing by Milla Nissi and Sharon Singleton
November 30, 2023
The Evolution of Chlorohydrination Process for Manufacturing PO
PUdaily | Updated: November 30, 2023
On July 14, the National Development and Reform Commission issued the National Industrial Restructuring Guidance Catalogue (2023 Edition) to seek public comments. In the new edition of the Catalogue, PO projects using chlorohydrination process based on calcium saponification are included in the eliminated category for the petrochemical and chemical industries (such projects are required to be eliminated by December 31, 2025). Restrictions on PO projects using chlorohydrination process can be traced back to the National Industrial Restructuring Guidance Catalogue (2011 edition).By the end of 2022, the share of PO projects using chlorohydrination process in China had decreased to 27.1%.
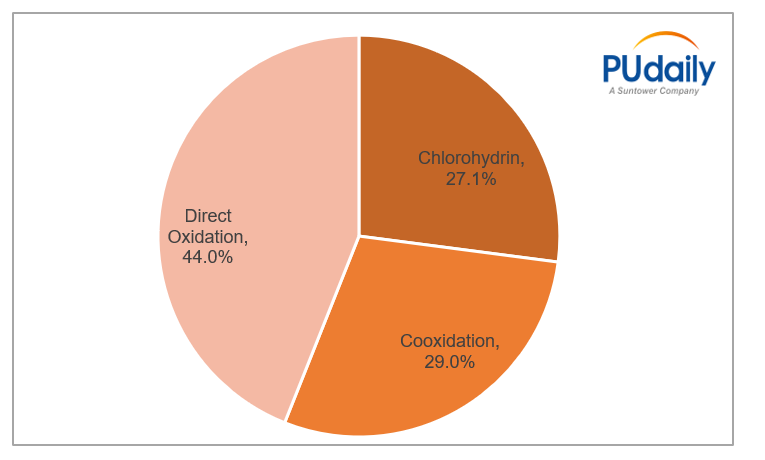
In chlorohydrination process, PO is manufactured using propylene and chlorine as the raw materials through chlorohydrination, saponification and rectification. Firstly, excess propylene is added to the mixture of water and chlorine to produce chloropropanol through chlorohydrination. The remaining propylene as well as hydrogen chloride and some organic chlorides (such as dichloropropane) produced in the reaction are discharged from the top of the reactor. and the hydrogen chloride and organic chlorides are removed through condensation for recovering the propylene. The chloropropanol solution containing 4% hydrochloric acid was discharged from the bottom of the reactor. Secondly, saponifier is added (caustic soda, instead of lime milk used in the traditional chlorohydrination process, is used in modified chlorohydrination process) to saponify chloropropanol for making crude PO. Thirdly, crude PO is transferred to the rectification column for separation and refining. The chlorohydrination process is composed of chlorohydrination, saponification and rectification.
As a mature technology, chlorohydrination process features production of a single product, easy operation of the facilities, low purity requirement for propylene and low building costs for the facilities. But it consumes a large amount of lime, chlorine and water, and results in a large amount of waste water and residue, which not only pollute the environment, but also cause corrosion to the equipment. Over the past decades, many firms at home and abroad have refined the process in different ways, represented by
1. Dow Chemical: The company replaces lime milk (Ca(OH)2) with electrolyte NaOH (mass fraction between 10% and 20%) in the saponification to significantly reduce the mass concentration of propanediol and dichloropropane in the saponified waste liquid and thus obtain relatively pure saline solution (NaCl and H2O). The saline solution is refined to make it saturated one, which is then transferred to the electrolytic bath for electrolysis that produces chlorine, hydrogen and sodium hydroxide. The chlorine is used as a raw material for the chlorohydrination process, and the sodium hydroxide is again used in the saponification. The recycling makes the process more economical. This refinement dramatically reduces the amount of waste water and residues (mainly composed of CaCl2) produced from saponification and as a result reduces the pollution of soil and water sources. However, the electrolytic process is energy-intensive.
2.ABB Lummus Global: The company comes up with the concept of closed-loop circulation, in which Cl2 and NaOH react with isobutanol to produce butyl hypochlorate as the chlorohydrating agent to reduce the use of Cl2; butyl hypochlorate react with propylene in the organic solvent to produce isobutanol and chloropropanol;and chloropropanol is saponified with the electrolyte to manufacture propylene oxide. Compared with the traditional chlorohydrination process, this refined process greatly reduces industrial wastewater, waste gases and residues. With a high mass concentration, the saline solution produced from saponification can be transferred to the electrolytic plant for electrolysis. The produced Cl2 and NaOH can be reused. But the process also has drawbacks, including large consumption of isobatyalcohol and high building costs for the facility.
A domestic firm has also developed its own environmentally friendly process for manufacturing PO, in which the recovered lime milk is saponified with the waste water and CaCl2 in the residual liquid. This process has been industrialized, producing significant social, environmental and economic benefits.
November 29, 2023
Tarragona Petrochemical Plant Fire: Industry Disruption and Safety Concerns
PUdaily | Updated: November 29, 2023
On the evening of November 22 (last Wednesday), a notable fire broke out in the ethylene tank area of the northern petrochemical facility in Tarragona, Spain, operated by Repsol. This unforeseen incident may have far-reaching effects on Repsol itself as well as the neighboring facilities of Covestro and Dow Chemical in the same industrial park.
Repsol’s industrial complex in Tarragona covers multiple sectors, ranging from the production of various petroleum products to industrial and transportation fuels, making it a large-scale operation. The cause of the fire is still unclear, but the company claimed that the ignition originated from a storage tank in the cooling area of the olefin plant, leading to an ethylene leak and subsequent ignition. The occurrence of this event prompts us to reflect on whether the petrochemical industry places sufficient emphasis on safety management while striving to improve production efficiency.
Fortunately, firefighters from the company and the professional fire brigade at the industrial park responded quickly and successfully controlled the fire, avoiding casualties. This accident has raised a high level of alertness among other companies in Tarragona. Covestro and Dow Chemical quickly halted production, including multiple grades of PO and polyols production. Covestro has four production sites in Spain, one of which is located in the Tarragona industrial park where the fire occurred. This site includes an MDI facility, a hydrochloric acid hub, and infrastructures for serving other companies within the park. Dow Chemical produces a variety of products including olefins, ethylene derivatives, pyrolysis products, and octenes at its Tarragona complex.
This fire has had a significant impact on the Spanish chemical industry, testing the crisis response capabilities of various companies and causing a production stagnation in Tarragona industrial park. As one of the leading chemical companies in Spain, Covestro’s production halt will undoubtedly have a ripple effect on the entire supply chain, further affecting the supply of chemical products in the international market.
Dow Chemical’s expansion plans at its Tarragona facility and the construction of Pack Studios demonstrate their confidence in the future market. Pack Studios, equipped with state-of-the-art film production and testing capabilities, is aimed at primary, secondary, and tertiary packaging applications. Pack Studios Tarragona will drive world-leading innovations in food and industrial packaging sectors, while also providing innovative adhesive solutions for global label customers. However, the recent unforeseen fire incident serves as a reminder that safety remains the utmost concern, even in highly modern petrochemical plants. The petrochemical industry must continually enhance safety training, strengthen equipment maintenance and monitoring, and reduce the probability of accidents through technological innovations.
Repsol has stated that an investigation has been initiated to determine the cause of the fire, and companies like Covestro and Dow will assess the losses and develop response plans. This event should also prompt other chemical companies to reevaluate their own safety systems to ensure not only efficient but also stable production.
November 28, 2023
Ingevity extends partnership with TRiiSO, LLC, expands Capa® distribution
footprint for customers in the United States and Canada
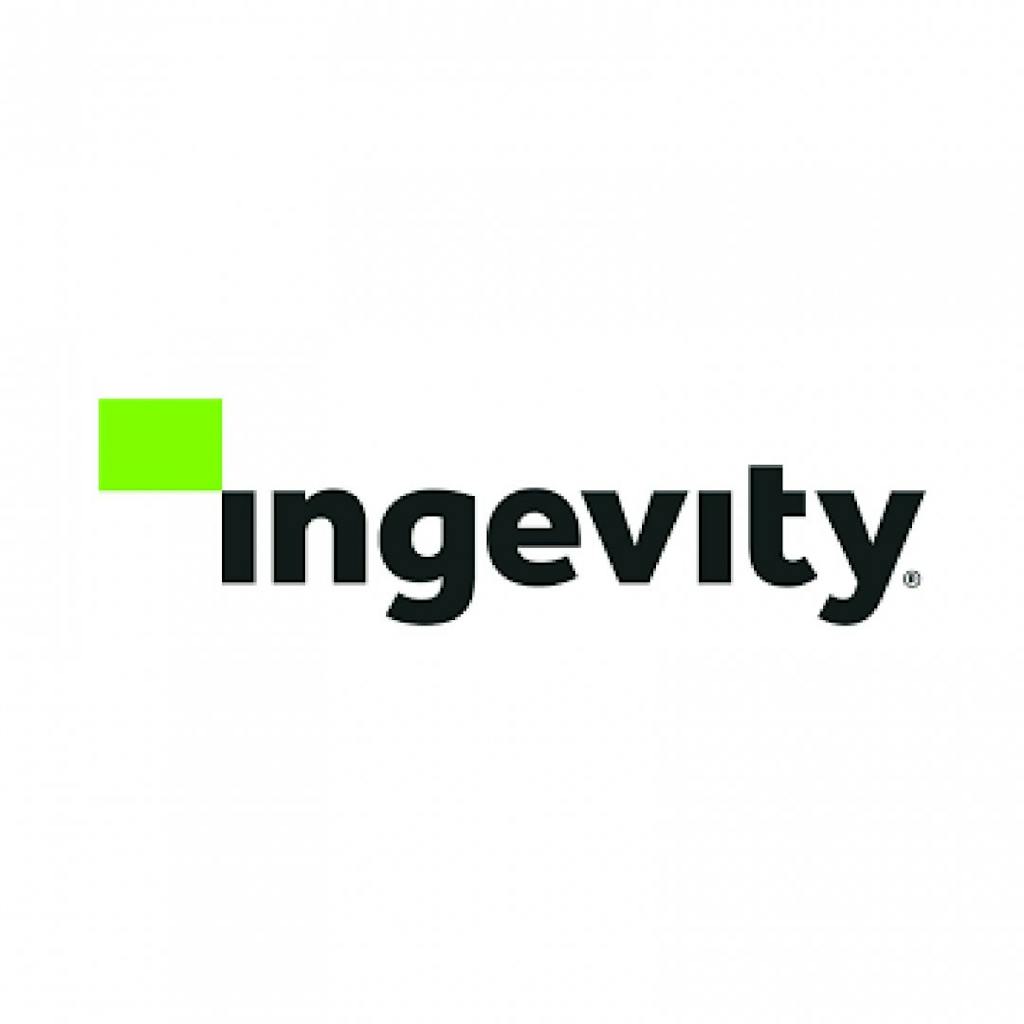
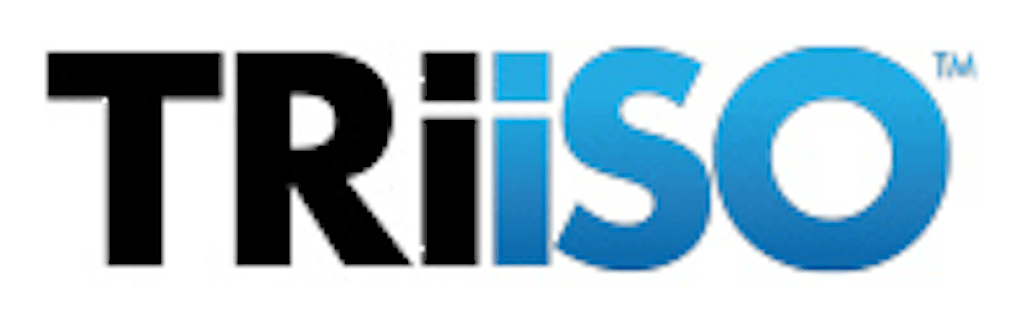
NORTH CHARLESTON, S.C., Nov. 28, 2023 – Ingevity Corporation (NYSE:NGVT) today
announced an extension of the distributorship with TRiiSO LLC (TRiiSO) to expand the
distribution footprint for the company’s Capa® products from the current western
United States (U.S.) to include all the U.S. and Canada. The new agreement will broaden
capabilities to serve existing Capa customers and support growth into new markets in
North America.
“Growing our partnership will allow for wider adoption of Ingevity’s Capa technology
and improved support for existing and new applications,” said Ingevity senior vice
president and president, Advanced Polymer Technologies, Steve Hulme. “Leveraging
TRiiSO’s nationwide reach and 50-year track record of supplying the coatings,
adhesives, sealants and elastomers (CASE) market strengthens our commitment to
providing current and future customers with innovative products and best in class
technical and customer service.”
“Ingevity’s focus on providing solutions to difficult formulating challenges aligns well
with TRiiSO’s technical support strengths,” said TRiiSO, vice president, Principal
Management, Mark McBee. “We are excited to expand our business footprint with
Ingevity throughout North America for the benefit of our existing and new customers
interested in high performance specialty polyols.”
The new distributorship agreement will take effect as of December 25, 2023.
Ingevity: Purify, Protect and Enhance
Ingevity provides products and technologies that purify, protect and enhance the world
around us. Through a team of talented and experienced people, we develop,
manufacture and bring to market solutions that help customers solve complex
problems and make the world more sustainable. We operate in three reporting
segments: Performance Chemicals, which includes specialty chemicals and pavement
technologies; Advanced Polymer Technologies, which includes biodegradable plastics
and polyurethane materials; and Performance Materials, which includes activated
carbon. Our products are used in in a variety of demanding applications, including
adhesives, agrochemicals, asphalt paving, bioplastics, coatings, elastomers, lubricants,
pavement markings, publication inks, oil exploration and production and automotive
components. Headquartered in North Charleston, South Carolina, Ingevity operates
from 31 countries around the world and employs approximately 1,900 people. The
company’s common stock is traded on the New York Stock Exchange (NYSE:NGVT). For
more information visit www.ingevity.com. Follow Ingevity on LinkedIn.
November 28, 2023
Panama Canal Congestion Causes MDI Price Increase in South America
PUdaily | Updated: November 27, 2023
The Panama Canal is Witnessing a Congestion with over 120 Ships Queueing
The Panama Canal Authority said on November 13 that approximately 126 ships were awaiting passage at the canal entrance, with potential waiting times of up to 12 days. To address the backlog of vessels, the authority holds auctions for those wishing to jump to the front of the line. In the latest auction, a Japanese energy group paid nearly USD 4 million to secure the crossing for its liquefied petroleum gas tanker, setting a new record and significantly increasing the transportation cost of transit goods.
El Niño Phenomenon Causes Congestion in the Panama Canal
Since the beginning of this year, the drought caused by the El Niño phenomenon has been affecting the water reservoir system of the Panama Canal, leading to a reduced supply of freshwater necessary for the operation of the locks. As a result, the Panama Canal Authority has repeatedly slashed the number of daily transiting vessels. Additionally, the authority has also lowered the permissible draft of ships, forcing vessels passing through the canal locks to reduce their weight or cargo load. This drove up the delivery time and logistics costs. In August, the canal experienced the first wave of congestion, with 200 vessels were floating at both ends of the dried up canal. Recently, the congestion issue has become more severe, significantly impacting global trade.

Panama Canal Congestion Affects Delivery Times and Costs between North and South America, Asia, and Europe
The Panama Canal, with a total length of 81.3 kilometers, connects the Atlantic Ocean and the Pacific Ocean. It is a lock-type canal where ships need to navigate through a series of locks to raise or lower the water level in order to traverse the canal located between the Central American mountain range. Alongside the Suez Canal, the Panama Canal plays a crucial role in global trade and economic development. The canal currently serves a total of 180 maritime routes that link 1,920 ports across 170 countries, the authority reported. The most significant trade routes serviced by the canal involve the US East Coast-Asia, US East Coast-South America West Coast, and Europe-South America West Coast routes.

MDI Prices are Moving up in South America
South American countries mainly import MDI from U.S., Europe, China, Japan, and South Korea. Due to the congestion in the Panama Canal and recent heavy rainfall in Brazil causing flooding in many ports, ships have been unable to dock, leading to delays in MDI imports and tight supply. As a result, some MDI suppliers have recently raised their quotations. PMDI prices in South America have moved up from the previous USD 1,900/tonne to the current range of USD 1,950-2,000/tonne.