The Urethane Blog
Everchem Updates
VOLUME XXI
September 14, 2023
Everchem’s exclusive Closers Only Club is reserved for only the highest caliber brass-baller salesmen in the chemical industry. Watch the hype video and be introduced to the top of the league: — read more
November 12, 2021
Plastics Industry Hurt by Lack Of Raw Materials Made of Oil
By Gerd Wilcke
- Nov. 30, 1973
About the ArchiveThis is a digitized version of an article from The Times’s print archive, before the start of online publication in 1996. To preserve these articles as they originally appeared, The Times does not alter, edit or update them.Occasionally the digitization process introduces transcription errors or other problems; we are continuing to work to improve these archived versions.
Randel Plastics, Inc., of Long Island City used to have 95 persons on its payroll. Last week there were only 48.
In Leominster, Mass., the Tucker Manufacturing Company has reduced its labor force by 15 per cent and has cut back from a three‐shift six‐day work week to 2.5 shifts five days a week.
What these two companies and hundreds of others have in common is that they cannot get enough raw materials made from oil to make their products. The products are plastics—in their multitude of variations that go into toys, automobiles, furniture, doorknobs or packaging materials.
The dramatic impact of the shortage was illustrated yesterday when the Chrysler Corporation announced a brief shutdown of four plants that manufacture compact cars. Chrysler said that the plants had experienced a shortage of plastic parts.
According to industry estimates, the average 1973‐model car used 138 pounds of plastics, and each 1974 model is using about 153 pounds.
In the New York area, the Plastics and Metal Producers Manufacturers Association said that its 174 member companies that normally employ 14,000 workers had to put 4,000 of them on short work weeks or on furlough.
PPG Industries, Inc., which is a joint venture partner in the Puerto Olefins Company at Penuelas, Puerto Rico, said it was being forced to shut down the plant for two weeks beginning Monday because of shortages of petrochemical raw materials.
American consumers facing the prospect of a cold winter may, at the moment, be more concerned over a cold home, school or an empty gasoline tank. But if Randel Plastics, Tucker Manufacturing and other fabricators are forced out of business the ripple effect could be enormous.
This is the third of a series of articles on the impact of the energy crisis on United States industries, which will appear at intervals.
Not only would thousands of products become scarce, but many thousands of people would lose their jobs.
Like the rest of the petrochemical industry, makers of plastics have to rely on oil for the hydrocarbons that go into building blocks for their products.
There are large companies such as E. I. du Pont de Nemours & Co., the Dow Chemical Company, the Monsanto Company, the Union Carbide Corporation, the Allied Chemical Corporation, or the Celanese Corporation that are major suppliers of building blocks such as ethylene, styrene, butadiene or phenol.
Although many of the major companies make their own end products, they are at the same time the key supply sources for companies such as Randel and Tucker Manufacturing.
Is the source drying up?
Executives of major companies do not deny that there is a shortage of key materials that has forced them to use an allocation system, However, they insist that they are attempting to be evenhanded in supplying domestic customers and are not ignoring them in order to make higher profits overseas.
Edward R. Kane, president of du Pont, and Werner C. Braun, the chief executive of Hercules, Inc., said in interviews the other day that there was no overt effort to ship more plastic resins overseas because of price controls in the United States. “The incidence of people taking advantage of the situation is small,” Mr. Kane said.
Mr. Braun said that there was no sudden upsurge in exports during the year and, although the dollar export volume was higher in reflection of monetary realignments, the physical volume of goods shipped showed a “normal” trade growth that was in line with domestic sales growth.
Plastics makers and fabricators, through the Society of the Plastics Industry, have argued for the lifting of price controls and, for the short term, a raw materials allocation plan patterned exactly on the basis of the 1972 distribution of oil and gas and all their derivatives.
Recent Study Cited
Ralph L. Harding Jr., president of the society, in this context cited a recent study by the Arthur D. Little Organization that pointed out that a 15 per cent cutback in feedstocks of raw materials to the petrochemical industry would mean the loss of 1.6 million jobs and a production loss of $65‐billion. The plastics industry accounts for about 25 per cent of the petrochemical industry and employs about 225,000 work ers. A 15 per cent cutback in feedstocks would, because of the domino effect, result in a $22‐billion curtailment in end products and in a loss of employment to 550,000 workers in both the plastic industry and the industries it supplies.
Theodore Riky, the president of Randel Plastics, does not think in these dimensions. He wants enough raw materials so he does not have to lay off more workers. He stressed that major resin suppliers had cut him off completely and that secondary suppliers were doing so little by little.
Can he afford going to the “open market,” a polite term used for the gray, or black. market?
‘45 Cents a Pound’
“If I pay cash on the line or by certified check before the supplier unloads a shipment, and paid 45 cents a pound for polypropylene and 53 cents for styrene, I might get the matesaid.
With the list price for both plastics standing at 17 cents a pound, Mr. Riky implied strongly that he could not afford to buy at such prices.
Sheldon Edelman is the president of the Plastics and Metal Producers Association, a group of fabricators in the plastics and metal fields. He complained bitterly that price controls came at a time when plastic resin prices were at a nine‐year low.
He said that companies buying directly from major suppliers were on allocation anywhere” in the 60 to 80 per cent area but that, as of last week, not even these reduced amounts reached the fabricators.
90 Per Cent of Capacity
In a recent study, Mr. Harding’s group said that, although production of plastic resins would increase this year by 10 to 15 per cent, to about 27 billion pounds, industry was operating at only 90 per cent of capacity.
As a result of the underutilization of capacity, the society said that most resin sales were on strict allocation by suppliers, there were significant shortages of formerly plentiful resin formulations, and there were severe shortages of certam formulations where intermediate, chemicals were not available, such as styrene monomer for polyester resin.
Mr. Harding has noted in this context that the plastics industry was facing a paradox. “Having reached the status of full membership in the industrial community,” he said, “the plastics industry finds itself threatened by limitations on its vitally needed raw material feedstocks.”
November 11, 2021
SABIC’S NEW NORYL™ POLYOL IMPROVES PERFORMANCE OF MDI-BDO CAST POLYURETHANES AND OFFERS ALTERNATIVE TO TDI-MOCA CURED SYSTEMS
11/11/2021
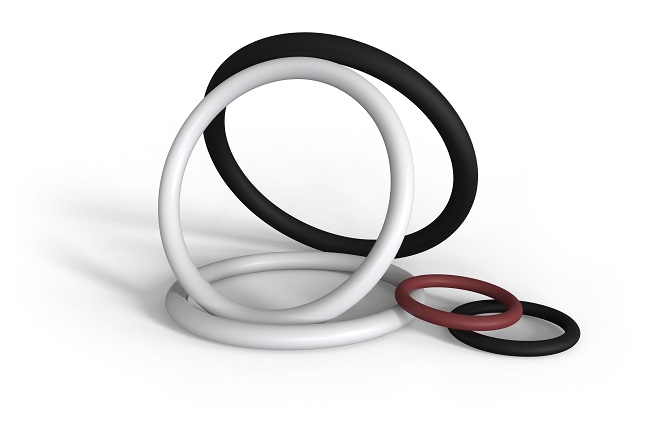
Home > News & Media > Latest News > SABIC’S NEW NORYL™ POLYOL IMPROVES PERFORMANCE OF MDI-BDO CAST…
SABIC, a global leader in the chemical industry, today announced that its recently launched NORYL™ AP2001G aromatic polyol can significantly improve the performance of hot cast polyurethanes (PUs) based on methylene diphenyl diisocyanate (MDI) and polytetramethylene ether glycol (PTMG). By boosting the hardness, toughness and stiffness properties of cast PU by double digits, NORYL AP2001G polyol can enable MDI formulations cured with 1,4-butanediol (BDO) to deliver equivalent or better performance compared to toluene diisocyanate (TDI) and PTMG PU formulations cured with MOCA (4,4′-methylene bis(ortho-chloroaniline)).
Due to increasing scrutiny in the use of MOCA as a substance of very high concern (SVHC) in the European Union, many PU manufacturers have adopted alternative formulations, including MDI-BDO. However, existing MDI-BDO systems pose performance challenges including lower mechanical and chemical properties vs. TDI-MOCA systems. SABIC’s NORYL AP2001G polyol for MDI-BDO systems addresses both the SVHC issue and performance deficiencies of existing materials, providing formulators with an alternative solution to TDI formulations and an opportunity to reduce or eliminate MOCA.
“As manufacturers began to transition away from SVHCs, SABIC understood the need to assist customers with this challenge,” said Antonello Cerullo, Ph.D., senior business development manager, SABIC. “We collaborated with Troy Polymers to validate the notable performance benefits of our new NORYL polyol for MDI-BDO systems. Thanks to our innovative new modifier, customers may now achieve results comparable to – or even better than – what they experienced with TDI-MOCA and MDI-BDO formulations, while staying ahead of the tighter restrictions that are being placed on the MOCA curative.”
Validating Performance Properties vs. MDI-BDO PUs
SABIC engaged Troy Polymers, a leading research and development laboratory based in Madison Heights, Mich., in the United States, to formulate PU samples using NORYL AP2001G polyol and conduct extensive testing and validation. The results showed that NORYL AP2001G polyol (at a loading of 5.6 percent) improved several properties of MDI-BDO cast PU formulations.
The SABIC modifier delivered up to a 30 percent increase in toughness, up to a 26 percent boost in tensile stress at break, up to an 8 percent improvement in elongation at break, and up to a 1.4 point jump in Shore D hardness.
Testing also revealed that NORYL AP2001G polyol can enhance hardness and toughness performance at high temperatures up to 70°C, which potentially allows MDI-BDO cast PU to be used in extreme conditions, such as for oil and gas exploration, gasketing and mining applications.
In terms of processability, when NORYL AP2001G polyol was added to the pre-polymer, the cast PU showed a longer pot life than a baseline MDI-BDO system. Details on the test methodology and results can be downloaded here.
“Based on our extensive experience in innovative polyurethane solutions, we have verified the benefits of SABIC’s NORYL AP2001G polyol for cast polyurethanes based on MDI-BDO systems,” said Aisa Sendijarevic, Ph.D., research director, Troy Polymers. “While MDI-BDO technology can replace TDI-MOCA in some applications, adding NORYL AP2001G polyol significantly improves MDI-BDO performance and offers an alternative that is free of substances of very high concern. Our test results indicate this SABIC polyol may enhance the performance and regulatory compliance of cast polyurethane.”
November 11, 2021
SABIC’S NEW NORYL™ POLYOL IMPROVES PERFORMANCE OF MDI-BDO CAST POLYURETHANES AND OFFERS ALTERNATIVE TO TDI-MOCA CURED SYSTEMS
11/11/2021
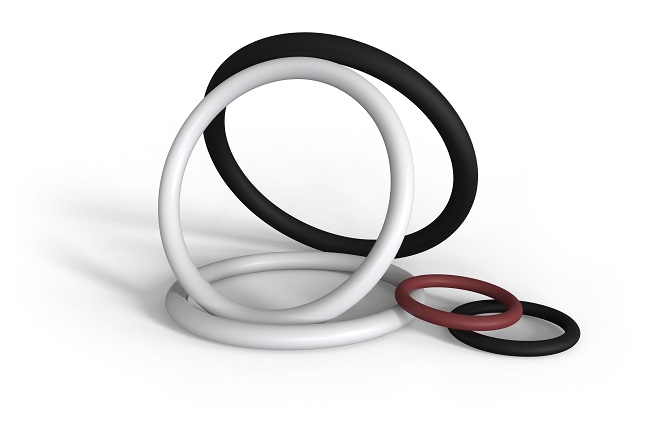
Home > News & Media > Latest News > SABIC’S NEW NORYL™ POLYOL IMPROVES PERFORMANCE OF MDI-BDO CAST…
SABIC, a global leader in the chemical industry, today announced that its recently launched NORYL™ AP2001G aromatic polyol can significantly improve the performance of hot cast polyurethanes (PUs) based on methylene diphenyl diisocyanate (MDI) and polytetramethylene ether glycol (PTMG). By boosting the hardness, toughness and stiffness properties of cast PU by double digits, NORYL AP2001G polyol can enable MDI formulations cured with 1,4-butanediol (BDO) to deliver equivalent or better performance compared to toluene diisocyanate (TDI) and PTMG PU formulations cured with MOCA (4,4′-methylene bis(ortho-chloroaniline)).
Due to increasing scrutiny in the use of MOCA as a substance of very high concern (SVHC) in the European Union, many PU manufacturers have adopted alternative formulations, including MDI-BDO. However, existing MDI-BDO systems pose performance challenges including lower mechanical and chemical properties vs. TDI-MOCA systems. SABIC’s NORYL AP2001G polyol for MDI-BDO systems addresses both the SVHC issue and performance deficiencies of existing materials, providing formulators with an alternative solution to TDI formulations and an opportunity to reduce or eliminate MOCA.
“As manufacturers began to transition away from SVHCs, SABIC understood the need to assist customers with this challenge,” said Antonello Cerullo, Ph.D., senior business development manager, SABIC. “We collaborated with Troy Polymers to validate the notable performance benefits of our new NORYL polyol for MDI-BDO systems. Thanks to our innovative new modifier, customers may now achieve results comparable to – or even better than – what they experienced with TDI-MOCA and MDI-BDO formulations, while staying ahead of the tighter restrictions that are being placed on the MOCA curative.”
Validating Performance Properties vs. MDI-BDO PUs
SABIC engaged Troy Polymers, a leading research and development laboratory based in Madison Heights, Mich., in the United States, to formulate PU samples using NORYL AP2001G polyol and conduct extensive testing and validation. The results showed that NORYL AP2001G polyol (at a loading of 5.6 percent) improved several properties of MDI-BDO cast PU formulations.
The SABIC modifier delivered up to a 30 percent increase in toughness, up to a 26 percent boost in tensile stress at break, up to an 8 percent improvement in elongation at break, and up to a 1.4 point jump in Shore D hardness.
Testing also revealed that NORYL AP2001G polyol can enhance hardness and toughness performance at high temperatures up to 70°C, which potentially allows MDI-BDO cast PU to be used in extreme conditions, such as for oil and gas exploration, gasketing and mining applications.
In terms of processability, when NORYL AP2001G polyol was added to the pre-polymer, the cast PU showed a longer pot life than a baseline MDI-BDO system. Details on the test methodology and results can be downloaded here.
“Based on our extensive experience in innovative polyurethane solutions, we have verified the benefits of SABIC’s NORYL AP2001G polyol for cast polyurethanes based on MDI-BDO systems,” said Aisa Sendijarevic, Ph.D., research director, Troy Polymers. “While MDI-BDO technology can replace TDI-MOCA in some applications, adding NORYL AP2001G polyol significantly improves MDI-BDO performance and offers an alternative that is free of substances of very high concern. Our test results indicate this SABIC polyol may enhance the performance and regulatory compliance of cast polyurethane.”
November 11, 2021
Evonik develops new chemical recycling process for polyurethane foam
By Mary Page Bailey | November 11, 2021
Evonik Industries AG (Essen, Germany) announced that it has developsx an efficient chemical recycling process for converting flexible polyurethane (PU) foams back to the original polyol raw material. Evonik’s new hydrolysis recycling process has the potential to achieve circularity in the flexible PU foam industry.
As the next phase of the development, Evonik will scale-up trials of its new process, which has been further strengthened by its partnership with The Vita Group, a leading provider of value-added and differentiated flexible PU foam products. The Vita Group has trialled the recycled polyols from Evonik’s hydrolysis process in several of its flexible foam applications.
According to the latest report from EUROPUR (European association of flexible polyurethane foam blocks manufacturers), some 40 million mattresses are discarded each year in Europe alone, with the majority ending up as landfill creating the equivalent of 600 kilotons of waste: including more than
300 kilotons of PU foam. With the potential to recycle the main component materials used in flexible PU foams and PU foam-based mattresses, Evonik’s process offers significantly higher use levels of the recycled polyol compared with existing commercialized technologies.
Evonik’s solution will contribute to the global flexible PU industry’s sustainability expectations of reducing waste and increasing the use of renewable raw materials in the production of its products. This enables Evonik to expand its position as a leading solutions provider for the PU industry and supports the entire Evonik Group’s objectives of establishing a fully functioning circular economy.
“It’s only by recycling products back to their raw materials and reusing them over and over again that we will enable a fully circular economy,” said Ralph Marquardt, Head of Evonik’s polyurethane additives business. “Our new hydrolysis process delivers recyclates of a quality and performance similar to that of virgin raw materials. Thus, innovative foam producers like our partner The Vita Group can meet their own sustainability targets, while continuing to deliver high-quality PU products.”
“The Vita Group is renowned for our long-history of innovation in sustainability and investing in circular economy products. We recycle and rebond over 30,000 tons of trim each year, as part of our dynamic sustainability agenda,” said Ian W. Robb, Group CEO for The Vita Group. “Sustainability and innovation are central principles of every aspect of our business. We see it as our responsibility to be at the vanguard of the development of eco-friendly technology within our industry. This hugely exciting partnership represents a key milestone on our journey to achieving the circular economy we are all striving for, and we look forward to working closely together with Evonik.”
November 11, 2021
Evonik develops new chemical recycling process for polyurethane foam
By Mary Page Bailey | November 11, 2021
Evonik Industries AG (Essen, Germany) announced that it has developsx an efficient chemical recycling process for converting flexible polyurethane (PU) foams back to the original polyol raw material. Evonik’s new hydrolysis recycling process has the potential to achieve circularity in the flexible PU foam industry.
As the next phase of the development, Evonik will scale-up trials of its new process, which has been further strengthened by its partnership with The Vita Group, a leading provider of value-added and differentiated flexible PU foam products. The Vita Group has trialled the recycled polyols from Evonik’s hydrolysis process in several of its flexible foam applications.
According to the latest report from EUROPUR (European association of flexible polyurethane foam blocks manufacturers), some 40 million mattresses are discarded each year in Europe alone, with the majority ending up as landfill creating the equivalent of 600 kilotons of waste: including more than
300 kilotons of PU foam. With the potential to recycle the main component materials used in flexible PU foams and PU foam-based mattresses, Evonik’s process offers significantly higher use levels of the recycled polyol compared with existing commercialized technologies.
Evonik’s solution will contribute to the global flexible PU industry’s sustainability expectations of reducing waste and increasing the use of renewable raw materials in the production of its products. This enables Evonik to expand its position as a leading solutions provider for the PU industry and supports the entire Evonik Group’s objectives of establishing a fully functioning circular economy.
“It’s only by recycling products back to their raw materials and reusing them over and over again that we will enable a fully circular economy,” said Ralph Marquardt, Head of Evonik’s polyurethane additives business. “Our new hydrolysis process delivers recyclates of a quality and performance similar to that of virgin raw materials. Thus, innovative foam producers like our partner The Vita Group can meet their own sustainability targets, while continuing to deliver high-quality PU products.”
“The Vita Group is renowned for our long-history of innovation in sustainability and investing in circular economy products. We recycle and rebond over 30,000 tons of trim each year, as part of our dynamic sustainability agenda,” said Ian W. Robb, Group CEO for The Vita Group. “Sustainability and innovation are central principles of every aspect of our business. We see it as our responsibility to be at the vanguard of the development of eco-friendly technology within our industry. This hugely exciting partnership represents a key milestone on our journey to achieving the circular economy we are all striving for, and we look forward to working closely together with Evonik.”