Polyurethane shows up in all sorts of consumer products: seat cushions in furniture and vehicles, car bumpers, shock-absorbing sneaker soles, and more. The global market for polyurethane was over $19 billion last year, and when those products wear out they generate vast quantities of waste—more than 1 million metric tons annually in the US alone. But the very thing that gives polyurethane its strength and durability—crosslinked polymer chains—makes it tough to reprocess into new products of comparable value. Instead of dumping it into landfills or “downcycling” it to make carpet padding, a group of researchers has shown they can break those crosslinks and reform the material to use in new products of similar commercial value to the original (ACS Cent. Sci., 2020, DOI: 10.1021/acscentsci.0c00083).
The Urethane Blog
Everchem Updates
VOLUME XXI
September 14, 2023
Everchem’s exclusive Closers Only Club is reserved for only the highest caliber brass-baller salesmen in the chemical industry. Watch the hype video and be introduced to the top of the league: — read more
May 6, 2020
Nudging reaction in reverse repurposes polyurethane foam
New polymer processing method offers a path to recycle a huge class of consumer goods
by Neil Savage, special to C&EN
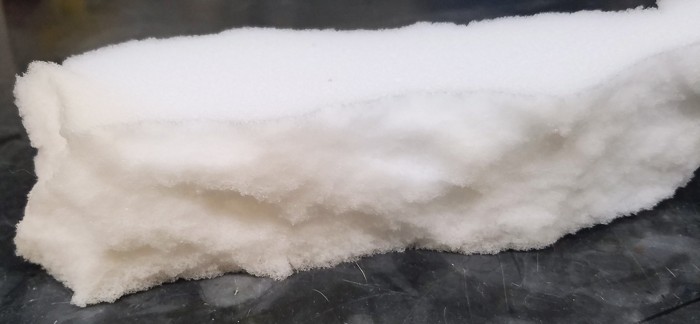
Polyurethane is a type of plastic known as a thermoset, which is cured by heat in a usually irreversible reaction. Dibutyltin dilaurate catalyzes the crosslinking reaction of the polyurethane chains as the material cures. But it turns out that at the right concentration and elevated temperatures, it both breaks and forms bonds within the material. So to break the material down, the researchers added the tin catalyst to rigid pieces of polyurethane foam and heated the material to 160° C. “We add a little bit more of [the catalyst] and that allows the reverse reaction to occur alongside the forward reaction,” says Daylan Sheppard, a graduate student in William Dichtel’s lab at Northwestern University and lead author of the paper. Because the reaction goes forward and backward, the polyurethane can be remolded.
The catalysis process breaks only a few of the crosslinks at a time, so the material never fully breaks down, Dichtel says, and the extrusion process puts mechanical stress on the material to change its overall shape. Making old polyurethane films into new films was relatively straightforward. But first attempts at reprocessing polyurethane foam into film or threadlike filaments led to cracks in the new material because of air trapped in the original foam. To combat that problem, the researchers used a pair of turning screws to force out the excess air as they extruded filaments or films.
When the team tested their method on actual consumer products, which can contain additives like flame retardants, they found such additives did not affect the reprocessing.
Steven Zimmerman, a chemist at the University of Illinois Urbana-Champaign, says the fact that researchers demonstrated the technique on commercial products is important because it shows the method can be applied to real-world materials. It’s also significant that the team recycled foams. “Previous work has focused on PU films, which are a lot easier to reprocess,” Zimmerman says. Foams “not only are most challenging but also represent the largest portion of the waste stream.” Foam is two-thirds of commercial polyurethane products.
Sheppard says producing recycled films is useful, because they’re used for rigid products such as bumpers, but given foam’s prevalence the team will work toward also making foam from the reprocessed material to broaden the types of products the process could create. They are also trying to find a more environmentally friendly catalyst without tin, Dichtel says. And they’re hoping this work might suggest new ways of dealing with other, chemically different crosslinked plastics. “The circularity of plastics really needs to improve,” Dichtel says, “and this is a small step in that very large goal.”
https://cen.acs.org/environment/recycling/Nudging-reaction-reverse-repurposes-polyurethane/98/i17
The Cincinnati Red Stockings played the first professional baseball game 146 years ago
The first pro baseball game was played 146 years ago

Up until the middle of the 19th century, baseball was an amateur’s game. A few players had gone professional — garnering salaries and whatnot — but until 1869, no team featured a professional starting nine. Enter the Cincinnati Red Stockings.
Led by Harry and George Wright (no, not those Wright brothers), the Red Stockings, precursors to MLB’s Cincinnati Reds, played baseball’s first pro game on May 4, 1869, against the amateur Great Westerns of Cincinnati — a game the Red Stockings won, 45-9. The team then kicked off pro ball’s first road trip, touring the country for 57 games that year and winning every single one.
Harry was responsible for founding the team, but George was, according to the National Baseball Hall of Fame, “baseball’s first superstar player.” George’s stats during that 57-0 streak: A .633 batting average while mashing 49 home runs. Perhaps it’s George who stands atop this celebratory cigar cutter:
146 years ago, when a team went on an impressive winning streak, they were awarded a Godzilla-sized baseball bat — or they were depicted in a woodcutting as being awarded a Godzilla-sized baseball bat, at least.
Maybe we should bring that tradition back:
The Cincinnati Red Stockings played the first professional baseball game 146 years ago
The first pro baseball game was played 146 years ago

Up until the middle of the 19th century, baseball was an amateur’s game. A few players had gone professional — garnering salaries and whatnot — but until 1869, no team featured a professional starting nine. Enter the Cincinnati Red Stockings.
Led by Harry and George Wright (no, not those Wright brothers), the Red Stockings, precursors to MLB’s Cincinnati Reds, played baseball’s first pro game on May 4, 1869, against the amateur Great Westerns of Cincinnati — a game the Red Stockings won, 45-9. The team then kicked off pro ball’s first road trip, touring the country for 57 games that year and winning every single one.
Harry was responsible for founding the team, but George was, according to the National Baseball Hall of Fame, “baseball’s first superstar player.” George’s stats during that 57-0 streak: A .633 batting average while mashing 49 home runs. Perhaps it’s George who stands atop this celebratory cigar cutter:
146 years ago, when a team went on an impressive winning streak, they were awarded a Godzilla-sized baseball bat — or they were depicted in a woodcutting as being awarded a Godzilla-sized baseball bat, at least.
Maybe we should bring that tradition back:
Jim Fitterling
Industrial Intermediates and Infrastructure operating EBIT was $175 million, down from the year ago period, as demand growth in the Industrial Solutions business was more than offset by market compression in polyurethane application, as well as equity losses.
The segment also benefited from lower year-over-year planned maintenance turnaround costs. The Polyurethane and Construction Chemicals business reported lower net sales, primarily driven by a lower global energy prices and decreased demand, particularly in furniture and bedding, automotive, appliance and aircraft deicing applications.
Also, we are taking actions to idle facilities or reduce operating rates in line with demand trends in the U.S., Europe and Latin America. We are working with our customers to get orders placed with enough lead times, so that we can make the best asset decisions across our network and manage bottlenecks in the supply chain to deliver products where it’s needed.
Our polyurethanes business has strong participation in Durable Goods segments, such as automotives, furniture and bedding, appliances and construction. These segments are being heavily impacted by government mandated shutdowns around the world, as a result, we are running our polyurethanes assets including propylene oxide and MDI at reduced operating rates.
And in silicones, we are running reduced rates across our global grid of siloxane trains and our Zhangjiagang production facility in China will remain down on an extended plant turnaround into May. We also benefit from full flexibility at our silicones finishing asset allowing us to quickly respond to demand in all formulated silicones applications around the world.
We are taking these actions with a thoughtful approach that will allow us to quickly respond as demand improves when economies around the world reopen, and while the timing and shape of a recovery remain uncertain these actions position Dow to emerge even stronger when the global economy rebound.
John Roberts
Thank you. And you all sound pretty well here, as well. So I am glad to hear that. Can you comment on other industry closures you might be seeing? We don’t usually think of Dow’s high cost although ethane is kind of flipped here currently, but, are we seeing other closures we haven’t heard about yet from competitors in the marketplace?
Jim Fitterling
Yes, John. Thanks for the question. We are not closing the high cost assets. We are closing the balance demand. So, look, all of these are reasonable cost assets, but the reality is, there has been a pretty significant amount of industrial capacity shutdown on the downstream. And so, we don’t feel like in this environment, really ploughing a lot of material into inventory is the right thing to do.
So, that’s why we are dialing back the capacity. I have seen some delays and indefinite suspensions of projects, there was one this week in Ohio, the Thai project that was going to go ahead. So, we are starting to see some of those kinds of announcements. We are seeing reduced rates across polyurethanes, across the globe basically and we’ve got polyurethanes MDI capacity down in China right now, not us, but competitors do.
Really to balance out the fact that downstream automotive and appliances and construction for insulation materials has been slow. So I think that’s what you are seeing. I think it has less to do with the cost position and more to do with the supply demand.
Arun Viswanathan
Hey, good morning. Thanks a lot. Thanks for what you are doing on the frontlines, as well. I guess, I just wanted to ask about both polyethylene and polyurethanes. Both markets has gone through some structural changes here polyethylene on the feedstock side and potentially demand side. Polyurethanes on the demand side with reduced demand for consumer discretionary items.
I guess, would you agree with those characterizations and I guess, when you think about that, thinking longer-term, do you foresee any changes in your strategy and polyurethane as you talked about adding Systems Houses and PE, you talked about selling. Are those still valid in this environment? Have you seen new customers trade down or change their strategy, as well? Thanks.
Jim Fitterling
Arun, I think, we’ll get back to the growth playbook as we mentioned in the script. And I think it’s just a matter of timing here. So, it doesn’t make sense right now to continue to plough cash and capacity when the demand in Europe and North America and Latin America has slowed down, because people are staying at home.
So that’s why we are taking some of the actions that we are taking right now. It’s just to balance that demand. But that demand will come back. People are not going to stay at home forever. We are helping governments right now with safe ways to return to work and we are operating safely. 14,000 Dow people go to the sites every day and we are operating safely and people are healthy.
So, we know it can be done. But it’s just going to take some time before the consumer confidence to come back and that’s why we are doing what we are doing. Downstream, expansions in our Industrial Solutions and in our Functional Silicones products are still continuing. Systems House will come back as the automotive business and the Installation and Construction business comes back and we’ll continue to look at downstream on plastics.
https://seekingalpha.com/article/4341619-dow-inc-dow-ceo-jim-fitterling-on-q1-2020-results-earnings-call-transcript?part=single
Jim Fitterling
Industrial Intermediates and Infrastructure operating EBIT was $175 million, down from the year ago period, as demand growth in the Industrial Solutions business was more than offset by market compression in polyurethane application, as well as equity losses.
The segment also benefited from lower year-over-year planned maintenance turnaround costs. The Polyurethane and Construction Chemicals business reported lower net sales, primarily driven by a lower global energy prices and decreased demand, particularly in furniture and bedding, automotive, appliance and aircraft deicing applications.
Also, we are taking actions to idle facilities or reduce operating rates in line with demand trends in the U.S., Europe and Latin America. We are working with our customers to get orders placed with enough lead times, so that we can make the best asset decisions across our network and manage bottlenecks in the supply chain to deliver products where it’s needed.
Our polyurethanes business has strong participation in Durable Goods segments, such as automotives, furniture and bedding, appliances and construction. These segments are being heavily impacted by government mandated shutdowns around the world, as a result, we are running our polyurethanes assets including propylene oxide and MDI at reduced operating rates.
And in silicones, we are running reduced rates across our global grid of siloxane trains and our Zhangjiagang production facility in China will remain down on an extended plant turnaround into May. We also benefit from full flexibility at our silicones finishing asset allowing us to quickly respond to demand in all formulated silicones applications around the world.
We are taking these actions with a thoughtful approach that will allow us to quickly respond as demand improves when economies around the world reopen, and while the timing and shape of a recovery remain uncertain these actions position Dow to emerge even stronger when the global economy rebound.
John Roberts
Thank you. And you all sound pretty well here, as well. So I am glad to hear that. Can you comment on other industry closures you might be seeing? We don’t usually think of Dow’s high cost although ethane is kind of flipped here currently, but, are we seeing other closures we haven’t heard about yet from competitors in the marketplace?
Jim Fitterling
Yes, John. Thanks for the question. We are not closing the high cost assets. We are closing the balance demand. So, look, all of these are reasonable cost assets, but the reality is, there has been a pretty significant amount of industrial capacity shutdown on the downstream. And so, we don’t feel like in this environment, really ploughing a lot of material into inventory is the right thing to do.
So, that’s why we are dialing back the capacity. I have seen some delays and indefinite suspensions of projects, there was one this week in Ohio, the Thai project that was going to go ahead. So, we are starting to see some of those kinds of announcements. We are seeing reduced rates across polyurethanes, across the globe basically and we’ve got polyurethanes MDI capacity down in China right now, not us, but competitors do.
Really to balance out the fact that downstream automotive and appliances and construction for insulation materials has been slow. So I think that’s what you are seeing. I think it has less to do with the cost position and more to do with the supply demand.
Arun Viswanathan
Hey, good morning. Thanks a lot. Thanks for what you are doing on the frontlines, as well. I guess, I just wanted to ask about both polyethylene and polyurethanes. Both markets has gone through some structural changes here polyethylene on the feedstock side and potentially demand side. Polyurethanes on the demand side with reduced demand for consumer discretionary items.
I guess, would you agree with those characterizations and I guess, when you think about that, thinking longer-term, do you foresee any changes in your strategy and polyurethane as you talked about adding Systems Houses and PE, you talked about selling. Are those still valid in this environment? Have you seen new customers trade down or change their strategy, as well? Thanks.
Jim Fitterling
Arun, I think, we’ll get back to the growth playbook as we mentioned in the script. And I think it’s just a matter of timing here. So, it doesn’t make sense right now to continue to plough cash and capacity when the demand in Europe and North America and Latin America has slowed down, because people are staying at home.
So that’s why we are taking some of the actions that we are taking right now. It’s just to balance that demand. But that demand will come back. People are not going to stay at home forever. We are helping governments right now with safe ways to return to work and we are operating safely. 14,000 Dow people go to the sites every day and we are operating safely and people are healthy.
So, we know it can be done. But it’s just going to take some time before the consumer confidence to come back and that’s why we are doing what we are doing. Downstream, expansions in our Industrial Solutions and in our Functional Silicones products are still continuing. Systems House will come back as the automotive business and the Installation and Construction business comes back and we’ll continue to look at downstream on plastics.
https://seekingalpha.com/article/4341619-dow-inc-dow-ceo-jim-fitterling-on-q1-2020-results-earnings-call-transcript?part=single