The Urethane Blog
Everchem Updates
VOLUME XXI
September 14, 2023
Everchem’s exclusive Closers Only Club is reserved for only the highest caliber brass-baller salesmen in the chemical industry. Watch the hype video and be introduced to the top of the league: — read more
November 18, 2021
Recticel enters into binding agreement with the Aquinos Group on the divestment of its Bedding business line
Regulated information, Brussels, 18/11/2021 — 07:00 CET, 18.11.2021
- Binding agreement signed with Aquinos Group, one of the largest European mattress and upholstery manufacturers
- Cash consideration based on an enterprise value of EUR 122.4 million on a cash and debt free basis
- Strong strategic fit, highly complementary geographic presence and product offerings
- Transaction subject to shareholder approval and customary closing conditions and consultations
Recticel announces that it has entered into a binding agreement to sell its Bedding business line to the Portuguese privately owned Aquinos Group.
Under the terms of the agreement the Bedding business line, will be sold to the Aquinos Group for an enterprise value of EUR 122.4 million. The transaction is expected to be closed in the first quarter of 2022, subject to customary closing conditions and consultations. The Nordic bedding activities will remain with Recticel and be integrated in the Living & Care segment of Recticel Engineered Foams. The net proceeds after transaction costs are expected to amount to EUR 97 million subject to closing adjustments. EUR 17.9 million IFRS 16 liabilities will be transferred as well.
Recticel’s Bedding business line develops and produces consumer-ready mattresses, slat bases and box springs, primarily marketed under popular brand names such as Beka®, Lattoflex®, Literie Bultex®, Schlaraffia®, Sembella®, Superba® and Swissflex®, as well as ingredient brands including GELTEX inside®. The Bedding activities currently consist of 9 manufacturing locations in seven EU countries – Austria (1), Belgium (2), Germany (2), Poland (1), Romania (1), Switzerland (1) and The Netherlands (1) – employing around 1,555 people. In 2020 the business line generated total sales of EUR 225.9 million, excluding the Nordic bedding activities.
The Aquinos Group, founded in 1985, is privately owned and headquartered in Sinde – Tábua (Portugal). Aquinos is one of the largest producers of furniture upholstery and mattresses in Europe with more than 3,300 employees and production sites in Portugal, France, and Poland. Aquinos, with 2020 annual sales of EUR 370 million, intends to further develop its bedding activities by complementing its existing product offering with strong brands, and expanding its customer base and geographic reach.
November 17, 2021
Huntsman’s Tony Hankins Inducted into UTECH Hall of Fame Maastricht, The Netherlands – On the opening day of the UTECH Europe Exhibition & Conference in Maastricht, The Netherlands, Tony Hankins, President of Huntsman’s Polyurethanes division, was inducted into the prestigious UTECH Hall of Fame.
At a special ceremony held on Tuesday 16 November, Tony Hankins joined a select group of senior polyurethane industry executives and thought leaders whose work in the world of polyurethanes is celebrated. The UTECH Hall of Fame recognizes leaders who have made a significant contribution to the global polyurethane industry and have spent at least 25 years working within the sector. Inductees are decided by an independent judging panel, which this year included representatives from Covestro, EUROPUR, ISOPA, Kingspan, Laaderberg, Polychemtech and Vitagroup.
Speaking at the event, Tony Hankins said: “I learned early in my career that the secret to longevity in this industry is to surround yourself with great people. So, I’d like to dedicate this award to the 4,000 employees in the Huntsman Polyurethanes business and thank them for their creativity and commitment. There are few industries in the world that are still going strong after 60 years; yet polyurethanes continues to enjoy sustainable growth. We undoubtedly have a bright future ahead.” Tony Hankins has worked in the polyurethanes industry for more than 30 years.
Huntsman’s global Automotive team was also shortlisted as a finalist in the UTECH Europe Automotive Awards for its ultra-low emission ACOUSTIFLEX® LE and RUBIFLEX® LE polyurethane-based foam systems for manufacturing sustainable car interiors.
November 17, 2021
Huntsman’s Tony Hankins Inducted into UTECH Hall of Fame Maastricht, The Netherlands – On the opening day of the UTECH Europe Exhibition & Conference in Maastricht, The Netherlands, Tony Hankins, President of Huntsman’s Polyurethanes division, was inducted into the prestigious UTECH Hall of Fame.
At a special ceremony held on Tuesday 16 November, Tony Hankins joined a select group of senior polyurethane industry executives and thought leaders whose work in the world of polyurethanes is celebrated. The UTECH Hall of Fame recognizes leaders who have made a significant contribution to the global polyurethane industry and have spent at least 25 years working within the sector. Inductees are decided by an independent judging panel, which this year included representatives from Covestro, EUROPUR, ISOPA, Kingspan, Laaderberg, Polychemtech and Vitagroup.
Speaking at the event, Tony Hankins said: “I learned early in my career that the secret to longevity in this industry is to surround yourself with great people. So, I’d like to dedicate this award to the 4,000 employees in the Huntsman Polyurethanes business and thank them for their creativity and commitment. There are few industries in the world that are still going strong after 60 years; yet polyurethanes continues to enjoy sustainable growth. We undoubtedly have a bright future ahead.” Tony Hankins has worked in the polyurethanes industry for more than 30 years.
Huntsman’s global Automotive team was also shortlisted as a finalist in the UTECH Europe Automotive Awards for its ultra-low emission ACOUSTIFLEX® LE and RUBIFLEX® LE polyurethane-based foam systems for manufacturing sustainable car interiors.
November 16, 2021
California Ports Defer Congestion Fee At The Last-Minute
by Tyler DurdenTuesday, Nov 16, 2021 – 02:40 PM
Authored by Greg Miller via FreightWaves.com,
Did ports defer fee plan because of progress or political peril?
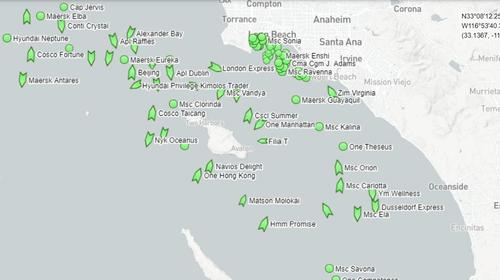
It came down to the wire, but the highly controversial Los Angeles/Long Beach congestion fee is not happening — at least, not yet.
The ports were scheduled to begin charging ocean carriers $100 per import container starting Monday for boxes moving by truck that dwelled for nine or more days, and for boxes dwelling for six or more days that move by rail. The charge was scheduled to escalate by $100 a day until the container left the property.
The ports announced Monday that they will “delay consideration” of the fee until Nov. 22, citing a 26% reduction in long-dwelling containers since the plan was announced on Oct. 25.
“There’s been significant improvement in clearing import containers from our docks in recent weeks,” said Port of Los Angeles Executive Director Gene Seroka. According to Port of Long Beach Executive Director Mario Cordero, “Clearly, everyone is working together to speed the movement of the cargo and reduce the backlog of ships off the coast as quickly as possible.”
Political risks of fee plan
Another reason the ports may not have pulled the trigger: the political peril of doing so.
Carriers explicitly stated that they would pass the cost along to importers. As of Monday, Long Beach had 19,656 containers on its terminals that would have been charged the late fee. There were at least 29,249 containers that would have incurred fees at the Port of Los Angeles (not including containers moving by rail that were between six and nine days late, which are not included in the data).
That means the aggregate fees to all carriers on Monday alone would have exceeded $4.8 million. And because the proposed fee would increase daily, the aggregate cost would have quickly risen into the tens of millions per day, and would have likely topped $100 million per day by the end of the first week.
During a conference call on Friday, Hapag-Lloyd CEO Rolf Habben Jansen warned, “If there’s cargo in those boxes that is not very valuable, you may end up with a lot of abandoned cargo that is going to stay at the terminal for much, much longer.”
Consultant Jon Monroe wrote in his weekly newsletter, “While I understand the intention, this is really a dumb idea for one good reason: The ports cannot measure the days that the container has been available to deliver.
“Under the current conditions, when a terminal discharges a container, it puts a percentage of the containers into closed lanes,” Monroe explained.
“Whenever a container is in a closed lane, it is unavailable for pickup by the trucker. No appointment can be made. Depending upon the terminal, anywhere from 20% to 80% of the containers will be put into a closed lane for an amount of time that varies. It is not unheard of for containers to sit in a closed lane for weeks. How will the ports account for containers that are in closed lanes?”
In a letter to the Federal Maritime Commission sent Monday, 85 business associations including the National Retail Federation wrote, “We are especially concerned about the announcements by the carriers that they intend to pass the charges through to the cargo owners.”
The groups warned that the new fee, if implemented, would “add substantial costs to the supply chain” due to “ongoing challenges that many cargo owners and drayage trucking companies are experiencing with the ability to retrieve cargo because of port congestion, restrictive empty return policies, and subsequent chassis shortages that result.”
During the inaugural meeting of the National Shippers Advisory Council on Oct. 27, various members called the Los Angeles/Long Beach congestion fee plan “catastrophic,” “crazy” and “out of left field.”
Long way to go
The two port bosses cited significant progress with clearing the terminals, yet the numbers show that most of the gains occurred in late October and early November. In recent days, the numbers have actually gotten worse.
In the port of Los Angeles, the number of containers dwelling nine day or more on Monday was up 18% from where it stood on Saturday and was the highest since last Wednesday. The total number of containers on the port — 76,613 — is higher than the number on Nov. 4.
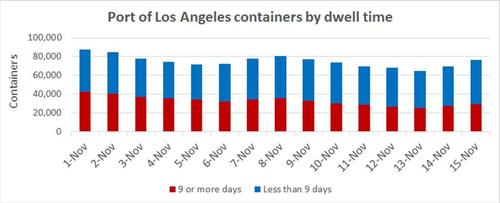
Chart: American Shipper based on data from Port of Los Angeles. Note: Containers dwelling six or more days that move by rail would also incur a fee.
According to Los Angeles’ data platform with Port Optimizer, 45% of containers at the APM Terminals facility were still past deadline, dwelling for nine days or more, as of Monday. The share of “late” containers was 40% at Everport Terminal Services and 48% at West Basin Container Terminal.
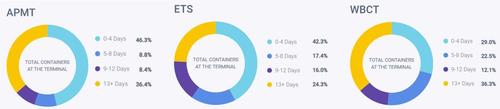
Charts: Port of Long Angeles, Port Optimizer
In the port of Long Beach, the number of containers that were past the time limit on Monday was up 14% from Saturday. The number is now higher than where it stood back on Nov. 6.
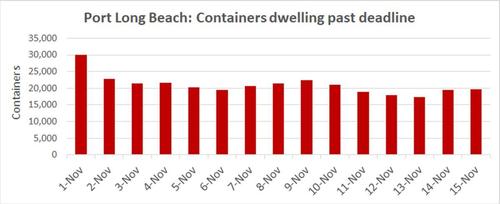
Chart: American Shipper based on data from Port of Long Beach. Note: containers past deadline include boxes moving by both rail and truck.
Meanwhile, cargo continues to flood into the two ports from the trans-Pacific trade lane.
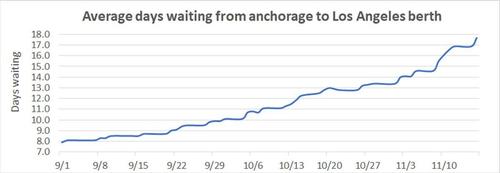
On Friday and Monday, yet another record was set for the number of container ships stuck at anchor or in holding patterns off the ports: 83. The average wait time at anchor for ships arriving in Los Angeles hit yet another fresh peak on Tuesday: 16.9 days.
November 16, 2021
California Ports Defer Congestion Fee At The Last-Minute
by Tyler DurdenTuesday, Nov 16, 2021 – 02:40 PM
Authored by Greg Miller via FreightWaves.com,
Did ports defer fee plan because of progress or political peril?
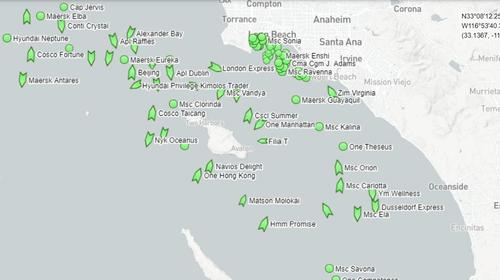
It came down to the wire, but the highly controversial Los Angeles/Long Beach congestion fee is not happening — at least, not yet.
The ports were scheduled to begin charging ocean carriers $100 per import container starting Monday for boxes moving by truck that dwelled for nine or more days, and for boxes dwelling for six or more days that move by rail. The charge was scheduled to escalate by $100 a day until the container left the property.
The ports announced Monday that they will “delay consideration” of the fee until Nov. 22, citing a 26% reduction in long-dwelling containers since the plan was announced on Oct. 25.
“There’s been significant improvement in clearing import containers from our docks in recent weeks,” said Port of Los Angeles Executive Director Gene Seroka. According to Port of Long Beach Executive Director Mario Cordero, “Clearly, everyone is working together to speed the movement of the cargo and reduce the backlog of ships off the coast as quickly as possible.”
Political risks of fee plan
Another reason the ports may not have pulled the trigger: the political peril of doing so.
Carriers explicitly stated that they would pass the cost along to importers. As of Monday, Long Beach had 19,656 containers on its terminals that would have been charged the late fee. There were at least 29,249 containers that would have incurred fees at the Port of Los Angeles (not including containers moving by rail that were between six and nine days late, which are not included in the data).
That means the aggregate fees to all carriers on Monday alone would have exceeded $4.8 million. And because the proposed fee would increase daily, the aggregate cost would have quickly risen into the tens of millions per day, and would have likely topped $100 million per day by the end of the first week.
During a conference call on Friday, Hapag-Lloyd CEO Rolf Habben Jansen warned, “If there’s cargo in those boxes that is not very valuable, you may end up with a lot of abandoned cargo that is going to stay at the terminal for much, much longer.”
Consultant Jon Monroe wrote in his weekly newsletter, “While I understand the intention, this is really a dumb idea for one good reason: The ports cannot measure the days that the container has been available to deliver.
“Under the current conditions, when a terminal discharges a container, it puts a percentage of the containers into closed lanes,” Monroe explained.
“Whenever a container is in a closed lane, it is unavailable for pickup by the trucker. No appointment can be made. Depending upon the terminal, anywhere from 20% to 80% of the containers will be put into a closed lane for an amount of time that varies. It is not unheard of for containers to sit in a closed lane for weeks. How will the ports account for containers that are in closed lanes?”
In a letter to the Federal Maritime Commission sent Monday, 85 business associations including the National Retail Federation wrote, “We are especially concerned about the announcements by the carriers that they intend to pass the charges through to the cargo owners.”
The groups warned that the new fee, if implemented, would “add substantial costs to the supply chain” due to “ongoing challenges that many cargo owners and drayage trucking companies are experiencing with the ability to retrieve cargo because of port congestion, restrictive empty return policies, and subsequent chassis shortages that result.”
During the inaugural meeting of the National Shippers Advisory Council on Oct. 27, various members called the Los Angeles/Long Beach congestion fee plan “catastrophic,” “crazy” and “out of left field.”
Long way to go
The two port bosses cited significant progress with clearing the terminals, yet the numbers show that most of the gains occurred in late October and early November. In recent days, the numbers have actually gotten worse.
In the port of Los Angeles, the number of containers dwelling nine day or more on Monday was up 18% from where it stood on Saturday and was the highest since last Wednesday. The total number of containers on the port — 76,613 — is higher than the number on Nov. 4.
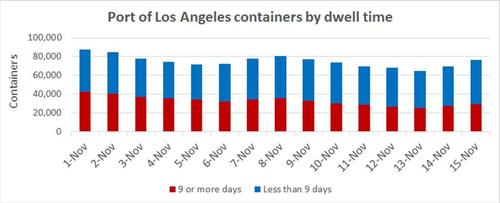
Chart: American Shipper based on data from Port of Los Angeles. Note: Containers dwelling six or more days that move by rail would also incur a fee.
According to Los Angeles’ data platform with Port Optimizer, 45% of containers at the APM Terminals facility were still past deadline, dwelling for nine days or more, as of Monday. The share of “late” containers was 40% at Everport Terminal Services and 48% at West Basin Container Terminal.
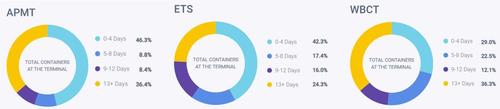
Charts: Port of Long Angeles, Port Optimizer
In the port of Long Beach, the number of containers that were past the time limit on Monday was up 14% from Saturday. The number is now higher than where it stood back on Nov. 6.
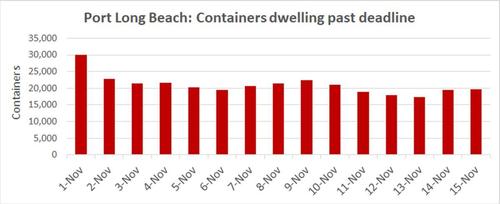
Chart: American Shipper based on data from Port of Long Beach. Note: containers past deadline include boxes moving by both rail and truck.
Meanwhile, cargo continues to flood into the two ports from the trans-Pacific trade lane.
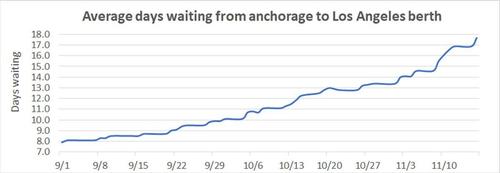
On Friday and Monday, yet another record was set for the number of container ships stuck at anchor or in holding patterns off the ports: 83. The average wait time at anchor for ships arriving in Los Angeles hit yet another fresh peak on Tuesday: 16.9 days.