The Urethane Blog
Everchem Updates
VOLUME XXI
September 14, 2023
Everchem’s exclusive Closers Only Club is reserved for only the highest caliber brass-baller salesmen in the chemical industry. Watch the hype video and be introduced to the top of the league: — read more
February 1, 2021
Case No. ADD (O.I.) 34/2019- Anti-dumping investigation concerning the imports of Toluene Di-Isocyanate from European Union, Saudi Arabia, Chinese Taipei and United Arab Emirates.
MINISTRY OF COMMERCE AND INDUSTRY
(Department of Commerce)
(DIRECTORATE GENERAL OF TRADE REMEDIES)
NOTIFICATION
FINAL FINDINGS
New Delhi, the 28th January, 2021
Case No. ADD (O.I.) 34/2019
Subject : Anti-dumping investigation concerning the imports of Toluene Di-Isocyanate from European Union, Saudi Arabia, Chinese Taipei and United Arab Emirates.
F. No. 6/43/2019-DGTR.—
A. BACKGROUND OF THE CASE
1. M/s Gujarat Narmada Valley Fertilizers & Chemicals Limited (hereinafter referred to as the “Applicant”) filed an application before the Designated Authority in accordance with Customs Tariff Act, 1975 (hereinafter also referred to as the “Act”) as amended from time to time and the Customs Tariff (Identification, Assessment and Collection of Antidumping Duty on Dumped Articles and for Determination of Injury) Rules, 1995 (hereinafter also referred to as the “Anti-Dumping Rules” or “Rules”) for initiation of anti-dumping investigation concerning the imports of Toluene Di-Isocyanate (hereinafter also referred to as the “product under consideration” or “PUC” or the “subject goods”) from European Union, Saudi Arabia, Chinese Taipei and United Arab Emirates (hereinafter also referred to as the “subject countries”).
2. The Authority on the basis of prima facie evidence submitted by the Applicant, issued a public notice vide Notification No. 6/43/2019-DGTR dated 31st January, 2020 in the Gazette of India Extraordinary initiating the investigation in accordance with Section 9A of the Act read with Rule 5 of the Rules to determine existence, degree and effect of the alleged dumping of the subject goods originating in or exported from the subject countries and to recommend the amount of anti-dumping duty (ADD), which if levied, would be adequate to remove the alleged injury to the Domestic Industry.
3. The Authority having regard to the Act and the Rules, considered it appropriate to recommend interim duties and issued Preliminary Findings vide Notification No. 6/43/2019-DGTR dated 4th September, 2020, recommending imposition of provisional ADD on the imports of the subject goods, originating in or exported from the subject countries. Accordingly, the Central Government vide Notification No.43/2020-Customs dated 2nd December, 2020 imposed provisional ADD on imports of the Toluene Di-Isocyanate from Chinese Taipei, European Union, Saudi Arabia and United Arab Emirates for a period of 6 months.
https://taxguru.in/custom-duty/anti-dumping-investigation-imports-toluene-di-isocyanate.html
January 30, 2021
Stepan Announces Acquisition of Aromatic Polyester Polyol Business from INVISTA
Fri, January 29, 2021, 6:09 PM·5 min read
NORTHFIELD, Ill., Jan. 29, 2021 /PRNewswire/ — Stepan Company (NYSE: SCL) today announced that it has purchased INVISTA’s aromatic polyester polyol business and associated assets. Included in the transaction are two manufacturing sites, one in Wilmington, NC (United States) and the other in Vlissingen (the Netherlands), and intellectual property, customer relationships, inventory and working capital. The business acquired has global sales of approximately $100 million. This acquisition was financed with cash on hand and is expected to be accretive to Stepan’s EBITDA margins.
“We are excited to add INVISTA’s polyester polyol capabilities to Stepan. This acquisition expands our manufacturing capability in both the United States and Europe, enhances our business continuity capabilities for the market and supports the growth of our global rigid polyol business. We expect that INVISTA’s available spare capacity, plus debottlenecking opportunities in both plants, will allow Stepan to support market growth in a capital efficient way,” said F. Quinn Stepan, Jr. Chairman and Chief Executive Officer of Stepan. “We believe the long-term prospects for rigid polyol use in insulation remain strong as energy conservation efforts and more stringent building codes should continue to drive market growth. Additionally, we believe the acquired technology will accelerate our product leadership initiatives, drive manufacturing efficiencies and output, and create increased value for the overall market. We look forward to providing the highest level of service to our new customers and are excited to add the new employees and the two new sites to our global polyester polyol manufacturing network.”
Management will provide more perspective on this acquisition as part of Stepan Company’s fourth quarter and full year 2020 results conference call on February 18, 2021.
https://finance.yahoo.com/news/stepan-announces-acquisition-aromatic-polyester-230900320.html
January 30, 2021
Stepan Announces Acquisition of Aromatic Polyester Polyol Business from INVISTA
Fri, January 29, 2021, 6:09 PM·5 min read
NORTHFIELD, Ill., Jan. 29, 2021 /PRNewswire/ — Stepan Company (NYSE: SCL) today announced that it has purchased INVISTA’s aromatic polyester polyol business and associated assets. Included in the transaction are two manufacturing sites, one in Wilmington, NC (United States) and the other in Vlissingen (the Netherlands), and intellectual property, customer relationships, inventory and working capital. The business acquired has global sales of approximately $100 million. This acquisition was financed with cash on hand and is expected to be accretive to Stepan’s EBITDA margins.
“We are excited to add INVISTA’s polyester polyol capabilities to Stepan. This acquisition expands our manufacturing capability in both the United States and Europe, enhances our business continuity capabilities for the market and supports the growth of our global rigid polyol business. We expect that INVISTA’s available spare capacity, plus debottlenecking opportunities in both plants, will allow Stepan to support market growth in a capital efficient way,” said F. Quinn Stepan, Jr. Chairman and Chief Executive Officer of Stepan. “We believe the long-term prospects for rigid polyol use in insulation remain strong as energy conservation efforts and more stringent building codes should continue to drive market growth. Additionally, we believe the acquired technology will accelerate our product leadership initiatives, drive manufacturing efficiencies and output, and create increased value for the overall market. We look forward to providing the highest level of service to our new customers and are excited to add the new employees and the two new sites to our global polyester polyol manufacturing network.”
Management will provide more perspective on this acquisition as part of Stepan Company’s fourth quarter and full year 2020 results conference call on February 18, 2021.
https://finance.yahoo.com/news/stepan-announces-acquisition-aromatic-polyester-230900320.html
January 30, 2021
Trans-Pacific Trade Crashes Into Max-Capacity Ceiling
by Tyler DurdenFriday, Jan 29, 2021 – 12:20
By Greg Miller of FreightWaves,
It’s official: Container volumes in the Asia-U.S. trans-Pacific trade have hit their limit. Massive port congestion in the ports of Los Angeles and Long Beach is forcing ocean carriers to take extreme measures. Sailings are now being “blanked” (canceled) not because of lack of demand, but because of lack of tonnage as ships are stuck awaiting berths.
When ships fall behind schedule due to long waits in port, carriers normally add “recovery vessels” to take their place and keep weekly services going. There are no recovery vessels left. According to Hapag-Lloyd, “as our fleets are fully deployed and stretched beyond capacity, this is regretfully currently not an option.”
As a result, Hapag-Lloyd has blanked 19 sailings in February. “It is important to emphasize that vessels will not be idling at any time and we will perform as many voyages as possible,” stressed the carrier. Hapag-Lloyd is a member of THE Alliance along with Ocean Network Express (ONE), Yang Ming and HMM.
‘Need-to-get-back-on-schedule blanks’
“Schedule reliability is horrible,” said Simon Sundboell, founder of eeSea, a company that analyzes ship schedules. “These are not ‘pull-out-capacity blanks.’ These are ‘need-to-get-back-on-schedule blanks,’” Sundboell told American Shipper.
Carriers usually blank sailings at this time of year due to lower exports during the Chinese New Year (CNY) holiday. Carriers initially opted to keep CNY sailings largely intact in order to clear the export pileup at Chinese ports. But the congestion in Los Angeles and Long Beach is leaving carriers short of ships. That means the pileup in Asia will take even longer to clear.
The eeSea platform provides complimentary access to real-time blank sailing data. The data as of Wednesday reveals an 11% dip in Asia-U.S. sailings in February versus January. This is despite continued high cargo demand.
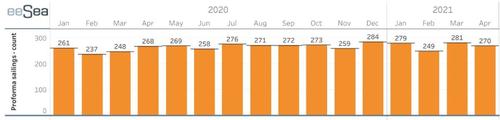
During a webinar presented by freight forwarder Flexport on Tuesday, Seaintelligence Consulting CEO Lars Jensen explained, “When you have all the vessels stuck waiting outside ports, they cannot make the return journey so they cannot start the sailing they were supposed to do. The blank sailings now are not a choice. They are an operational necessity.”
No letup in San Pedro Bay traffic jam
At any given time since the beginning of this year, there have been around 30 container ships stuck waiting at anchorages in San Pedro Bay offshore of the ports of Los Angeles and Long Beach.
The situation has not improved at all. According to the Marine Exchange of Southern California, there were 33 container ships at anchorages and 26 at berths on Wednesday. Including all ship types, there were 55 vessels at anchorages — a new record, with all Los Angeles/Long Beach anchorages full and all contingency anchorages off Huntington also full.San Pedro Bay container-ship positions Jan. 27 (Map: MarineTraffic)
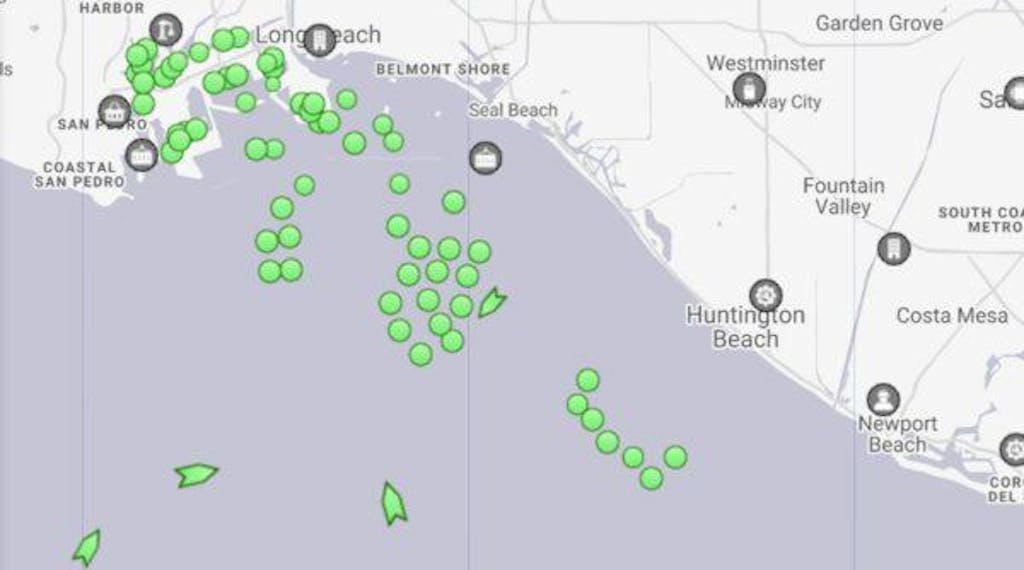
On Monday, many of those vessels had to leave anchorage and go to sea due to extreme storm conditions. Winds gusted to 55 mph and swells reached 15 feet. Marine Exchange Executive Director Kip Louttit exclaimed that he “could not recall a more complex situation with this many vessels and this bad a wind and sea condition for such a sustained period of time.”
Port congestion is being caused by high inbound volumes combined with surging COVID cases among dockworkers. A spokesperson for the ILWU dockworkers union told American Shipper that number of its members testing positive had risen to 803 as of Monday, up 16% from 694 as of Jan. 17.
“They can’t service the ships fast enough, which has led to waiting times of 10-14 days or even more, depending on the terminal,” said Nerijus Poskus, global head of ocean freight at Flexport.
“As of last week, there were almost 300,000 TEUs [twenty-foot equivalent units] waiting to get offloaded,” Poskus added.
Jensen put it another way. “It is the equivalent of pulling five full trans-Pacific services out of action as long as you have these waiting times,” he said. “The impact is massive.”
Deteriorating reliability, rising rolls
As previously reported by American Shipper, global schedule reliability has collapsed to around 50% versus normal levels of 70%-80%. Getting a box delivered on time is no better than a coin toss. In reality, the chance is much worse. Schedule reliability data doesn’t take into account blank sailings. Nor does it take into account cargo that is “rolled” — pushed off to a subsequent voyage.
Data on cargo rolls by the world’s top liners at the world’s top ports is compiled by Ocean Insights. According to Ocean Insights data released last week, the share of shipments that did not sail aboard their originally scheduled vessels rose to 37% in December. That’s up sharply from 29% in July and 25% in December 2019.
One importer moving goods from China via Los Angeles wrote to American Shipper: “We’re seeing over 60 days of additional transit time now. The entire process used to take 28 days. Now containers shipped in November have still not reached their final destination.”
Add it all up and U.S. consumers should see escalating shortages of goods on the shelves. That, in turn, should fuel import demand even further into 2021.
Light at the end of the tunnel?
One of the central drivers of today’s capacity crunch is a shortfall of containers. Or rather, a shortfall of containers positioned in the right place.
But there are some glimmers of hope. Data on container-equipment availability is tracked by the Container x-Change Container Availability Index. Availability of 40-foot high cubes (40HCs) remains extremely low. But availability of 20-foot dry cargo (20DC) and 40-foot standard dry cargo (40DC) units improved markedly this month.
The index “finally shows a positive trend,” asserted David Amezquita, head of data insights at Container xChange. The upcoming CNY period could “finally be the turning point,” added the company.
An index level below 0.5 is considered a shortage. In the third week of January, the index in Shanghai for 20DCs was up to 0.34 and for 40DCs to 0.37. The index for 40HCs was still a very low 0.11.(Chart: Container x-Change)
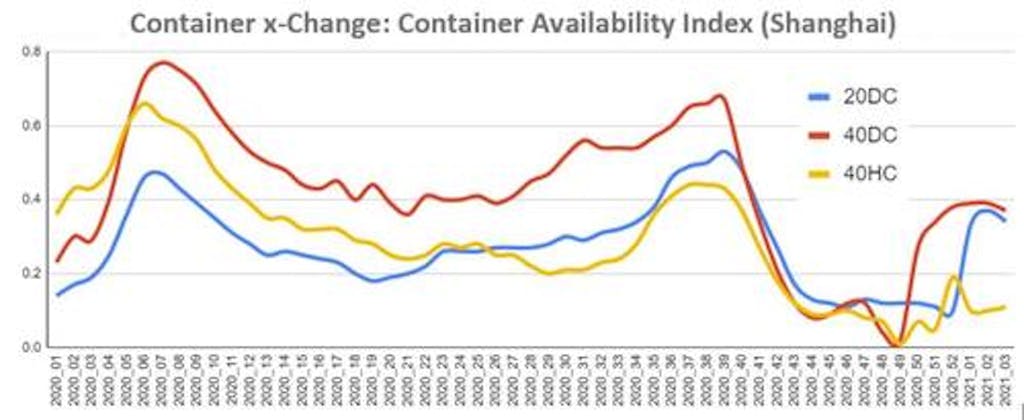
Getting back to normal
Jensen expressed confidence that the container-equipment challenge will be resolved fairly soon. Chinese factories have been busy churning out new boxes.
“What’s happening now is exactly the same scenario we saw in 2010 after the financial crisis. If you look at 2010, they went on a building spree. It took about three months from when the problem arose to when it was resolved. If we put that in the context we have now, this should be resolved by Chinese New Year.
“The wild card this time around is the port congestion because that ties up a significant part of the ability to reposition the empty containers back into balance. That could delay things somewhat,” acknowledged Jensen.
As more containers are manufactured, liners should simultaneously work to get sailings back on schedule. “It appears the carriers plan to use the post-Chinese New Year period to get their vessels back on schedule,” said Jensen. “If that works out and if we get the port congestion sorted out — which is a big if — we could get back to normal levels [of service reliability] within a few months. But that’s the optimistic view.”
https://www.zerohedge.com/markets/trans-pacific-trade-crashes-max-capacity-ceiling
January 30, 2021
Trans-Pacific Trade Crashes Into Max-Capacity Ceiling
by Tyler DurdenFriday, Jan 29, 2021 – 12:20
By Greg Miller of FreightWaves,
It’s official: Container volumes in the Asia-U.S. trans-Pacific trade have hit their limit. Massive port congestion in the ports of Los Angeles and Long Beach is forcing ocean carriers to take extreme measures. Sailings are now being “blanked” (canceled) not because of lack of demand, but because of lack of tonnage as ships are stuck awaiting berths.
When ships fall behind schedule due to long waits in port, carriers normally add “recovery vessels” to take their place and keep weekly services going. There are no recovery vessels left. According to Hapag-Lloyd, “as our fleets are fully deployed and stretched beyond capacity, this is regretfully currently not an option.”
As a result, Hapag-Lloyd has blanked 19 sailings in February. “It is important to emphasize that vessels will not be idling at any time and we will perform as many voyages as possible,” stressed the carrier. Hapag-Lloyd is a member of THE Alliance along with Ocean Network Express (ONE), Yang Ming and HMM.
‘Need-to-get-back-on-schedule blanks’
“Schedule reliability is horrible,” said Simon Sundboell, founder of eeSea, a company that analyzes ship schedules. “These are not ‘pull-out-capacity blanks.’ These are ‘need-to-get-back-on-schedule blanks,’” Sundboell told American Shipper.
Carriers usually blank sailings at this time of year due to lower exports during the Chinese New Year (CNY) holiday. Carriers initially opted to keep CNY sailings largely intact in order to clear the export pileup at Chinese ports. But the congestion in Los Angeles and Long Beach is leaving carriers short of ships. That means the pileup in Asia will take even longer to clear.
The eeSea platform provides complimentary access to real-time blank sailing data. The data as of Wednesday reveals an 11% dip in Asia-U.S. sailings in February versus January. This is despite continued high cargo demand.
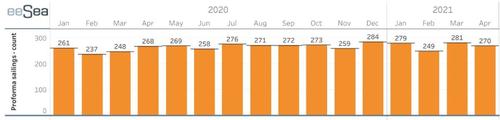
During a webinar presented by freight forwarder Flexport on Tuesday, Seaintelligence Consulting CEO Lars Jensen explained, “When you have all the vessels stuck waiting outside ports, they cannot make the return journey so they cannot start the sailing they were supposed to do. The blank sailings now are not a choice. They are an operational necessity.”
No letup in San Pedro Bay traffic jam
At any given time since the beginning of this year, there have been around 30 container ships stuck waiting at anchorages in San Pedro Bay offshore of the ports of Los Angeles and Long Beach.
The situation has not improved at all. According to the Marine Exchange of Southern California, there were 33 container ships at anchorages and 26 at berths on Wednesday. Including all ship types, there were 55 vessels at anchorages — a new record, with all Los Angeles/Long Beach anchorages full and all contingency anchorages off Huntington also full.San Pedro Bay container-ship positions Jan. 27 (Map: MarineTraffic)
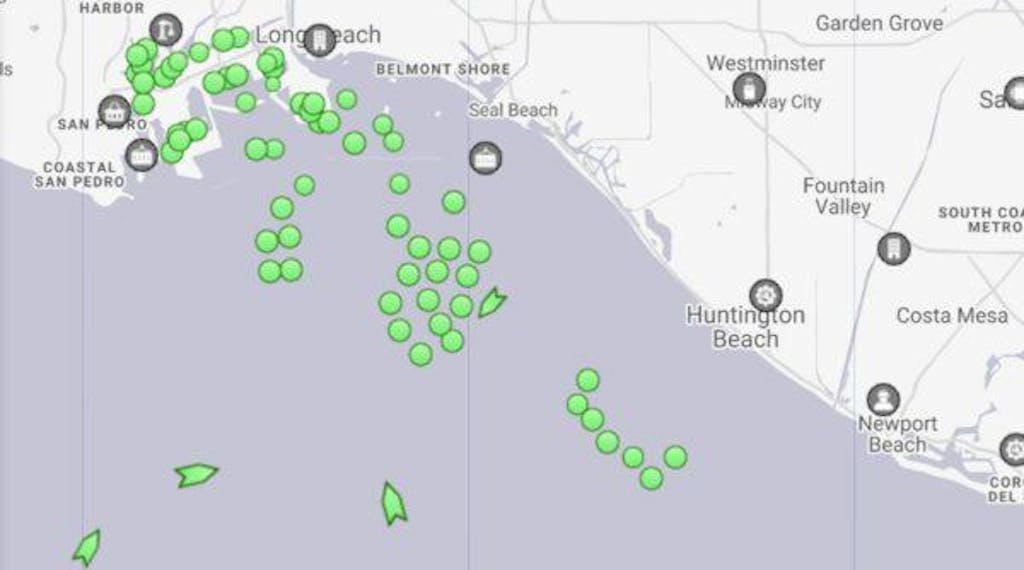
On Monday, many of those vessels had to leave anchorage and go to sea due to extreme storm conditions. Winds gusted to 55 mph and swells reached 15 feet. Marine Exchange Executive Director Kip Louttit exclaimed that he “could not recall a more complex situation with this many vessels and this bad a wind and sea condition for such a sustained period of time.”
Port congestion is being caused by high inbound volumes combined with surging COVID cases among dockworkers. A spokesperson for the ILWU dockworkers union told American Shipper that number of its members testing positive had risen to 803 as of Monday, up 16% from 694 as of Jan. 17.
“They can’t service the ships fast enough, which has led to waiting times of 10-14 days or even more, depending on the terminal,” said Nerijus Poskus, global head of ocean freight at Flexport.
“As of last week, there were almost 300,000 TEUs [twenty-foot equivalent units] waiting to get offloaded,” Poskus added.
Jensen put it another way. “It is the equivalent of pulling five full trans-Pacific services out of action as long as you have these waiting times,” he said. “The impact is massive.”
Deteriorating reliability, rising rolls
As previously reported by American Shipper, global schedule reliability has collapsed to around 50% versus normal levels of 70%-80%. Getting a box delivered on time is no better than a coin toss. In reality, the chance is much worse. Schedule reliability data doesn’t take into account blank sailings. Nor does it take into account cargo that is “rolled” — pushed off to a subsequent voyage.
Data on cargo rolls by the world’s top liners at the world’s top ports is compiled by Ocean Insights. According to Ocean Insights data released last week, the share of shipments that did not sail aboard their originally scheduled vessels rose to 37% in December. That’s up sharply from 29% in July and 25% in December 2019.
One importer moving goods from China via Los Angeles wrote to American Shipper: “We’re seeing over 60 days of additional transit time now. The entire process used to take 28 days. Now containers shipped in November have still not reached their final destination.”
Add it all up and U.S. consumers should see escalating shortages of goods on the shelves. That, in turn, should fuel import demand even further into 2021.
Light at the end of the tunnel?
One of the central drivers of today’s capacity crunch is a shortfall of containers. Or rather, a shortfall of containers positioned in the right place.
But there are some glimmers of hope. Data on container-equipment availability is tracked by the Container x-Change Container Availability Index. Availability of 40-foot high cubes (40HCs) remains extremely low. But availability of 20-foot dry cargo (20DC) and 40-foot standard dry cargo (40DC) units improved markedly this month.
The index “finally shows a positive trend,” asserted David Amezquita, head of data insights at Container xChange. The upcoming CNY period could “finally be the turning point,” added the company.
An index level below 0.5 is considered a shortage. In the third week of January, the index in Shanghai for 20DCs was up to 0.34 and for 40DCs to 0.37. The index for 40HCs was still a very low 0.11.(Chart: Container x-Change)
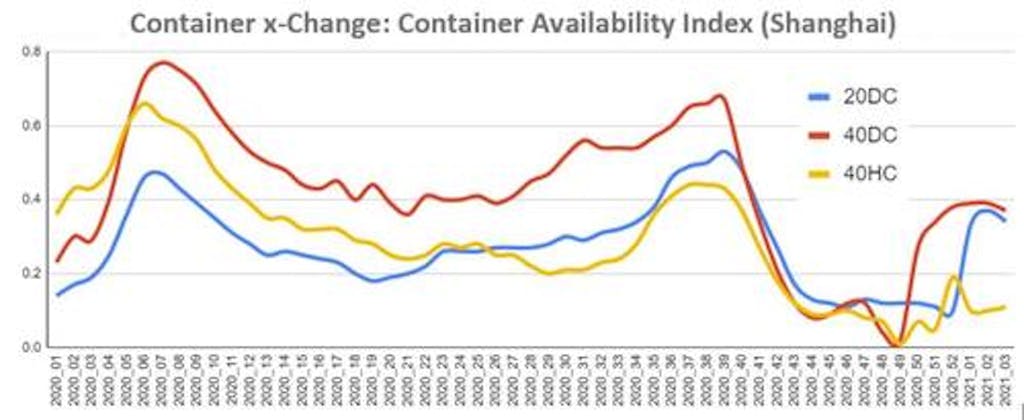
Getting back to normal
Jensen expressed confidence that the container-equipment challenge will be resolved fairly soon. Chinese factories have been busy churning out new boxes.
“What’s happening now is exactly the same scenario we saw in 2010 after the financial crisis. If you look at 2010, they went on a building spree. It took about three months from when the problem arose to when it was resolved. If we put that in the context we have now, this should be resolved by Chinese New Year.
“The wild card this time around is the port congestion because that ties up a significant part of the ability to reposition the empty containers back into balance. That could delay things somewhat,” acknowledged Jensen.
As more containers are manufactured, liners should simultaneously work to get sailings back on schedule. “It appears the carriers plan to use the post-Chinese New Year period to get their vessels back on schedule,” said Jensen. “If that works out and if we get the port congestion sorted out — which is a big if — we could get back to normal levels [of service reliability] within a few months. But that’s the optimistic view.”
https://www.zerohedge.com/markets/trans-pacific-trade-crashes-max-capacity-ceiling