The Urethane Blog
Everchem Updates
VOLUME XXI
September 14, 2023
Everchem’s exclusive Closers Only Club is reserved for only the highest caliber brass-baller salesmen in the chemical industry. Watch the hype video and be introduced to the top of the league: — read more
May 20, 2024
Chimcomplex Wraps Up €2.43M Project for Making Polyols from Natural Oils
Published on 2024-05-17. Edited By : SpecialChem
TAGS: Sustainability / Natural Solutions
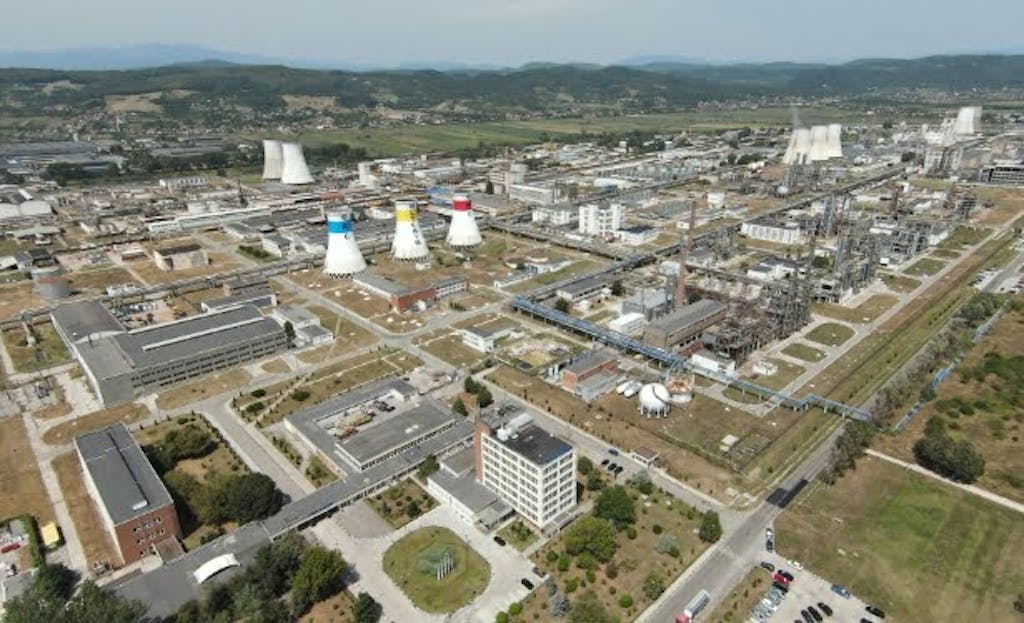
Chimcomplex SA Borzești concludes the project to make the production processes ecofriendly and align the company’s activities with circular economy principles.
The project was implemented at the Rm Vâlcea plant. The total eligible value of the project is €2,431,000, with non-repayable financial assistance amounting to €1,215,000.
Green Polyols from Castor Oil, Soybean Oil, and Palm Oil
Investing in innovative technology for environmentally friendly polyol production was the next necessary step after the inauguration of one of Europe’s most modern polyol plants in 2022.
This €40 million investment increased the company’s production capacity to over 187,000 tons per year. These innovative “green polyols,” produced using the new technology, replace the petrochemical components of conventional polyols with less polluting alternatives or natural oils such as castor oil, soybean oil, and palm oil. Further down the production chain, these “green polyols” are used to create soft foams for pillows, mattresses, and other automotive components.
The impact of this investment is significant:
- The new production line will allow Chimcomplex to increase its existing capacity by an additional 17,000 tons of special polyols annually. After client testing, these new polyols will enter serial production, significantly reducing their environmental impact due to the nature of the technologies and raw materials used in manufacturing.
- Replacing conventional polyols with the new special types will reduce CO2 emissions by up to 3,400 tons annually.
- The company’s competitiveness will improve through portfolio expansion.
- The new facility enhances the company’s adaptability to customized product needs for individual clients. Product design will be done collaboratively with customers, adapting formulas based on their requirements.
- Current and future clients can purchase the new “Made in Rm. Vâlcea” polyols, reducing the carbon footprint of their final products and labeling them as environmentally friendly.
Amalia Ionescu, project manager, stated, “This new investment completed at the Rm. Vâlcea plant reflects the company’s commitment to sustainability, innovation, and development. We thank Innovation Norway for supporting the project. Over the past 5 years, Chimcomplex specialists from the Advanced Polyol Research and Development Center have created new experimental polyol types, which can now be rapidly tested and widely used by our clients. Fine chemicals add value to Romania overall and to consumers in particular. We all desire safer and healthier products for everyday use. You can rely on the expertise of chemists to find solutions for environmental challenges and develop technologies that reduce our planet’s negative impact.”
The project was carried out in partnership with International Development Norway, a Norwegian organization with over 20 years of experience in international projects focused on eco-business best practices.
https://chimcomplex.com/docs/press-releases/
HISTORY
1954
CHIMCOMPLEX was founded in Borzesti, Onesti, Bacau County.
1966-1970
In Râmnicu Vâlcea, was established in 1966 SC OLTCHIM SA under the name of Râmnicu Vâlcea Chemical Plant.
In the two industrial platforms, the needed installations were put into operation for chlorosodium products, oxo alcohols, vinyl chloride, polyvinyl chloride and HCH lindane, all based on foreign licenses.
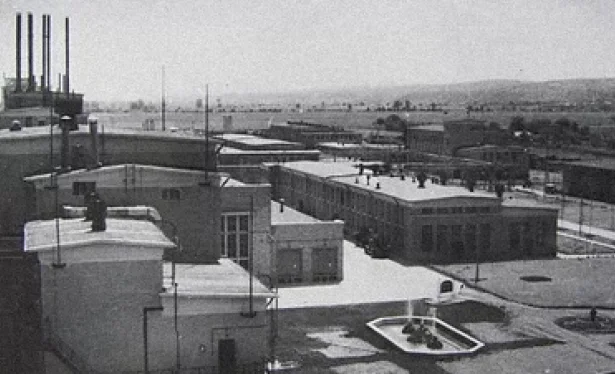
1971-1980
At Oltchim takes place the development of the production profile from the first stage. New production capacities are put into operation and the product range is diversified with chlorinated solvents, propylene oxide, propylene glycols, polyethers, polyols, phosgene;
1981-1990
At Oltchim, new capacities were put into operation for organic intermediates (amines, chloroformates) and a wide range of pesticides.
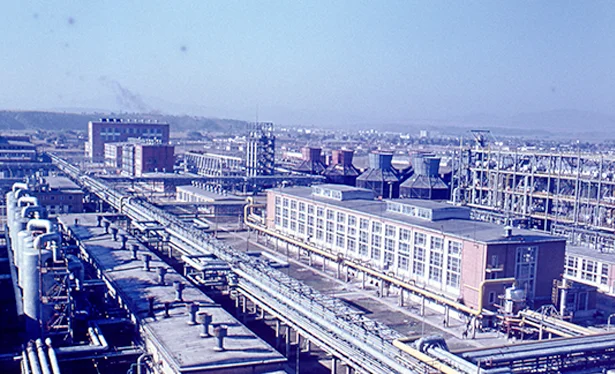
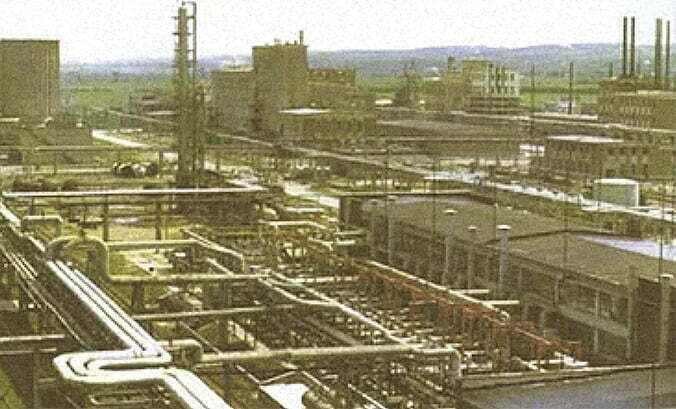
1990
Successive investments take place in production at Borzești Chemical Plant: electrolysis, inorganic chlorides, solvents, PVC, alkylamines, and pesticides.
1991
The Borzești Chemical Plant becomes Chimcomplex SA Borzești with registration number at the trade register J04/493/1991. The financial capital was mostly owned by the state.
1991-1999
The products portfolio has been diversified on both platforms, over 40 basic products in over 78 assortments were developed. Thus we have been producing PVC, polyol polyether, plasticizers, pesticide formulas and formulas for processing plastic materials.
In 1997 Oltchim is listed on the capital market in the first category of the Bucharest Stock Exchange.
2000-2003
Meant the fulfillment of some strategic objectives for the development of Oltchim: modernizations (oxo-alcohols installation, ion exchange membrane electrolysis), commissioning of new installations (caustic soda flakes and pearls, phthalic anhydride, dioctyl phthalate, water demineralization, waste incineration) ) and capacity expansions to existing facilities (propene oxide, flexible polyols, PVC).
2003
Chimcomplex SA Borzești was privatized by Mr. Ștefan Vuza, saving it from bankruptcy. In the first three years, Ștefan Vuza made investments of over 25 million euro. Another 285 million euros were invested in the next 10 years. Mr. Vuza’s strategy also aimed at acquiring Oltchim, which will be the core of the Romanian Chemical Company.
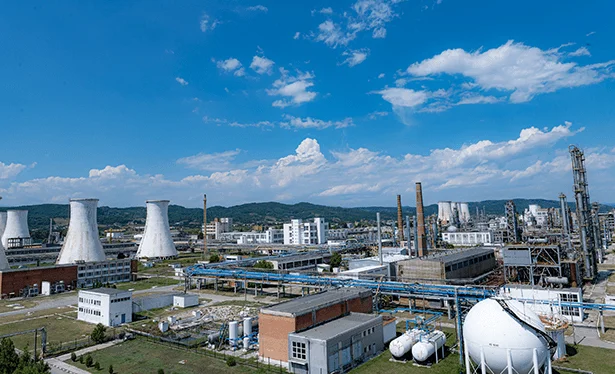
2004-2012
At Oltchim, capacity modernizations and extensions were carried out at the existing technological installations: propene oxide, polyol-polyethers, PVC and a new waste incineration plant were put into operation, as well as an industrial lime plant. In 2010 the turnover decreases due to the lack of ethylene – the main raw material used in the production process.
2013
Oltchim goes into insolvency;
2018
In December 2018, Mr. Ștefan Vuza managed, by contracting an international loan of 1 64 million euros, to acquire Oltchim’s Rm. Vâlcea assets. He thus saved this plant from bankruptcy on the last hundred meters. The financial transaction was spectacular, Mr. Vuza managed to convince a consortium of banks to finance it, although Chimcomplex had an annual turnover of 50 million euros, with a normal profit rate in the chemistry of 10% and a profit of 5 million euros per year. By acquiring these assets, Chimcomplex has strengthened its position as a producer and supplier of chemicals in Europe and formed the nucleus of the new chemical plant in Romania, around which 10 companies are currently gravitating.
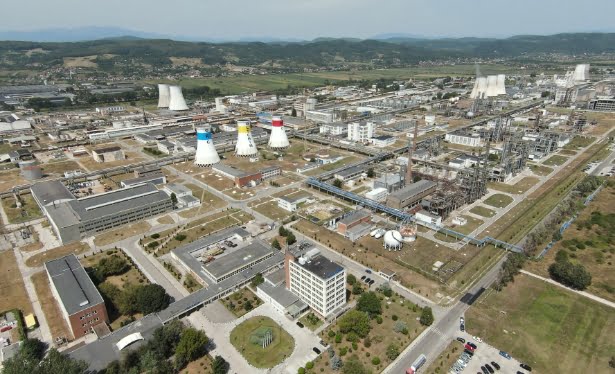

2019-2020
Chimcomplex achieved all its goals, including financial ones, but the path was very different from how it was planned. The company had taken decisive actions and had shown a lot of resilience during COVID-19. At the same time, we encouraged employees, focusing on customer needs and supporting its communities. Chimcomplex closed the year with a stronger balance sheet, ready to accelerate its strategy and realize bold plans for the future.
2021
Chimcomplex stocks recorded the largest increase in history with 1.200% in 2021. It was the biggest increase on all European stock exchanges. Turnover doubled. Net profit increased by over 510% in 2021 compared to 2020. The financial results obtained as a reaction of the synergies between the two plants in Onești and Rm. Vâlcea provided additional liquidity that Chimcomplex
used to make investments and repay all bank loans in advance.
Chimcomplex acquired part of the assets of CET Govora with the idea of building a production capacity of thermal agents in a cogeneration plant. The Romanian Chemical Company has grown and has been reorganised into 8 divisions, to develop efficiently. Thus we have The Chemical Division, The Energy Division, The Research Division, The International Trade and Business Division, The Maintenance and Support Services Division, The Logistics and Transport Division, The Green Division and The White Division.
We also obtained accreditation for the Chimcomplex Academy – an authorized center for training, improvement, and development of competencies for attracting and maintaining staff.
The refinancing carried out in 2021 led to a 6-fold decrease in financial expenses and Chimcomplex achieved all its business objectives.
2022
Chimcomplex consolidated its service portfolio by acquiring Sistemplast S.A. Râmnicu Vâlcea, a company located on the Oltchim platform, that specialized in providing integrated solutions for mechanics, design, construction, verification and monitoring of industrial works.
After an investment of 40 million euros, Chimcomplex inaugurated a new polyol production plant. Thus, in Romania, almost 9% of the European production of polyols will be produced, which will bring the company to the 6th place among the top producers in Europe.
2023
At Rm. Vâlcea will be put into operation the largest high-efficiency cogeneration plant built in Romania, in the last 11 years. The three cogeneration groups have an annual energy capacity of 49.5 MWh, which is used on the platform. The cogeneration plant produces both electricity and thermal energy in the form of technological steam and hot water, with an overall efficiency of 90.5%. This investment of 40 million euros helps us eliminate our dependence on polluting alternatives, but also to reduce CO2 emissions by more than 88,000 tons/year, thus becoming a more responsible and sustainable company.
Chimcomplex is a consolidated company with growth potential and a market value of between 2 and 2.2 billion euros, considering both multiples of EBITDA in the chemical industry and the value on the stock market. Chimcomplex is today the largest producer of green hydrogen in Eastern Europe, with an annual production of over 6,000 tons. It is the only company in Europe’s 10 SE countries with real potential to use hydrogen as a raw material for green chemicals.
Currently, projects of over 55 million euros are in the final execution phase and projects worth over 125 million euros are being prepared and started.
May 20, 2024
MOL’s €1.3 billion polyol complex in Tiszaújváros inaugurated
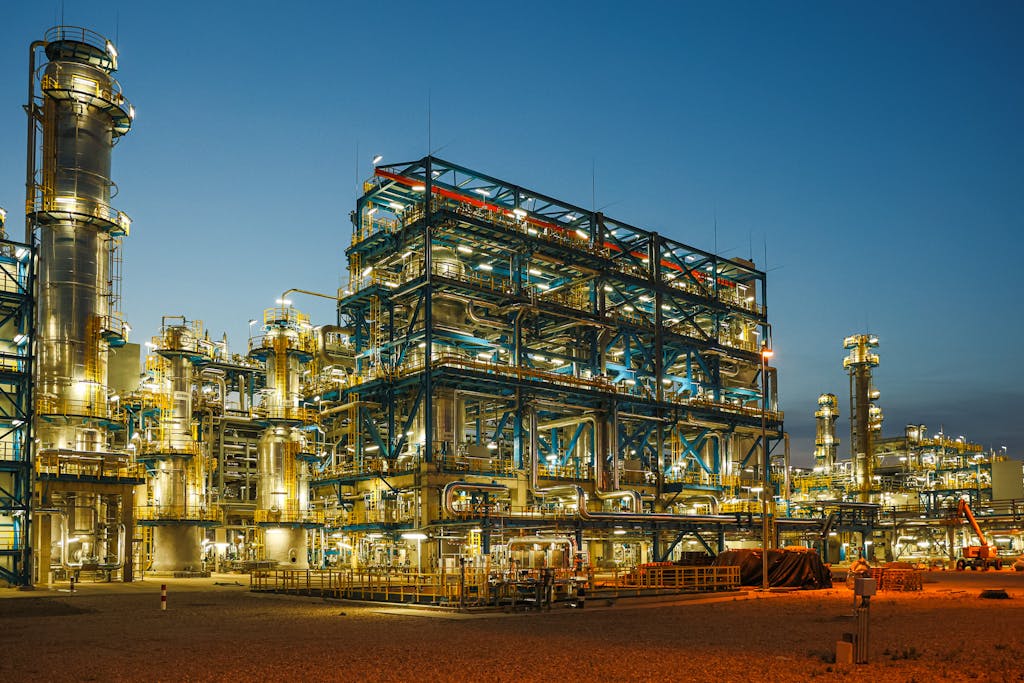
- The €1.3 billion project is MOL’s largest organic investment to date, for which it has also received support from the Hungarian state
- The complex will produce raw materials for durable plastic consumer goods such as bed mattresses, moulded car seats, insulation for houses and elastic rubber soles for sports shoes
- Thanks to the innovative technology of Germany’s thyssenkrupp Uhde and Evonik, the plant is operating with the most advanced technology available
Tiszaújváros, May 14, 2024 – MOL’s EUR 1.3 billion polyol complex in Tiszaújváros, boasting a capacity of around 200,000 tonnes of polyol per year, has been inaugurated. The ceremony, addressed by Prime Minister of Hungary Viktor Orbán, MOL’s Chairman-CEO, Zsolt Hernádi, and thyssenkrupp Board member Ilse Henne, marks a significant milestone for the company. MOL Group stands as the sole entity in Hungary and in Central and Eastern Europe to cover the entire value chain, from petroleum processing to polyol production (a widely used plastic raw material).
MOL Group held an inauguration ceremony in Tiszaújváros to celebrate the completion of its largest organic investment, the polyol complex. MOL, thyssenkrupp and Evonik IP signed the licence agreement in summer 2017, and the foundation stone of the complex was laid in September 2019.
The main units were transported to Tiszaújváros between 2019 and 2020, mainly by water, and were followed by the completion of the complex’s hydrogen peroxide, propylene oxide, polyol and propylene glycol plants. In addition to the four main plants, a pilot polyol plant, a quality assurance laboratory and, in Százhalombatta, a Research and Development Center were also built.
“I am proud that we have completed the polyol complex. It was a true international team effort, a great collaboration involving thousands of people over the past six years that enabled us to deliver MOL Group’s largest investment ever, perhaps the biggest development in modern Hungarian history. We have come a long way, but the road ahead is even longer. The polyol complex will significantly strengthen our company’s position and competitiveness, with the entire value chain from petroleum processing to polyol production. This investment has put Tiszaújváros back on the map of the European chemical industry, making it one of the most important industrial centers in the region. It will enhance the industrial competitiveness of our country and could catalyze economic growth as well. Through this investment, Hungary will be stronger, as MOL’s success is the success of the whole country,” said Zsolt Hernádi, Chairman and CEO of MOL Group.
“With this new MOL polyol-complex we establish new standards in terms of efficiency, environmental friendliness and automation by combining proven technologies with innovative solutions”, said Nadja Håkansson, CEO of thyssenkrupp Uhde. “We are grateful for the deep and trustful partnership with MOL. This polyol plant is a true landmark project and a great demonstration of how we at thyssenkrupp Uhde enable the industrial green transformation. With fully integrated and highly automated plant units, the valuable polyol chemicals will be produced in a highly efficient and sustainable way.”
The project involved an international team of thousands of experts, with engineering design work carried out in Germany, Thailand, India and Hungary. The plant equipment came from 24 countries. The construction of the complex involved 75 000 cubic metres of concrete, 13 000 tonnes of steel, 2 500 kilometres of cable and 700 km of pipelines laid in more than 18 million working-hours. The Hungarian government contributed with €131.5 million to the project: a €93.6 million corporate tax credit, which can be claimed once the investment is operational, and a €37.9 million investment grant based on an individual government decision.
Polyol is one of the most sought-after plastics raw materials, used in a wide range of industries from car manufacturing to clothing and insulation. Polyurethane is made from polyol and is the base material for many of the durable consumer goods that everyone encounters in their everyday lives.
Polyurethane made from polyol is needed:
- for the production of foam mattresses, bed mattresses, foam for comfortable seating on sofas and armchairs, and rigid foams for insulating refrigerators;
- for the production of insulating materials used in the construction industry, whether for the insulation of the facade of a building or a pipeline;
- for the production of sealants and adhesives familiar from DIY stores, and the elastic rubber soles of running shoes.
The Tiszaújváros plant will produce polyol using one of the most efficient and environmentally friendly methods available today. According to MOL’s calculations, the plant will contribute nearly EUR 150 million annually to the MOL Group’s financial results and will provide long-term employment for nearly 300 people.
MOL Group has been strengthening its chemical business for almost ten years: the new butadiene extraction plant was completed in 2015 with a HUF 35 billion investment, followed by the synthetic rubber (S-SBR) plant in 2018 with a HUF 100 billion investment. In 2016, the company announced a major strategic shift to prepare for the energy transition and the post-fossil fuel world by expanding its portfolio. As part of the third and largest wave of investment in the petrochemicals business, next to the polyol complex, the polypropylene plant is the most important element, which is a HUF 65 billion investment, and there are nearly EUR 2 billion of life cycle investments that will secure the long-term future of the chemicals business.
About MOL Group
MOL Group is an international, integrated oil, gas, petrochemicals and consumer retail company, headquartered in Budapest, Hungary. It is active in over 30 countries with a dynamic international workforce of 24,000 people and a track record of more than 100 years. MOL Group operates three refineries and two petrochemicals plants under integrated supply chain-management in Hungary, Slovakia and Croatia, and owns a network of almost 2400 service stations across 10 countries in Central & South Eastern Europe. MOL’s exploration and production activities are supported by more than 85 years’ experience in the field of hydrocarbons and 30 years in the injection of CO2. At the moment, there are production activities in 8 countries and exploration assets in 10 countries.
MOL is committed to transform its traditional fossil-fuel-based operations into a low-carbon, sustainable business model and aspires to become net carbon neutral by 2050 while shaping the low-carbon circular economy in Central-and Eastern Europe.
About thyssenkrupp Uhde
thyssenkrupp Uhde combines unique technological expertise and decades of global experience in the engineering, procurement, construction and service of chemical plants. We develop innovative processes and products for a more sustainable future and thus contribute to the long-term success of our customers in almost all areas of the chemical industry. Our portfolio includes leading technologies for the production of base chemicals, fertilizers and polymers as well as complete value-chains for green hydrogen and sustainable chemicals. www.thyssenkrupp-uhde.com
May 20, 2024
ISM: Economic improvement to continue through 2024
By Larry Adams
May 17, 2024 | 6:28 am CDT
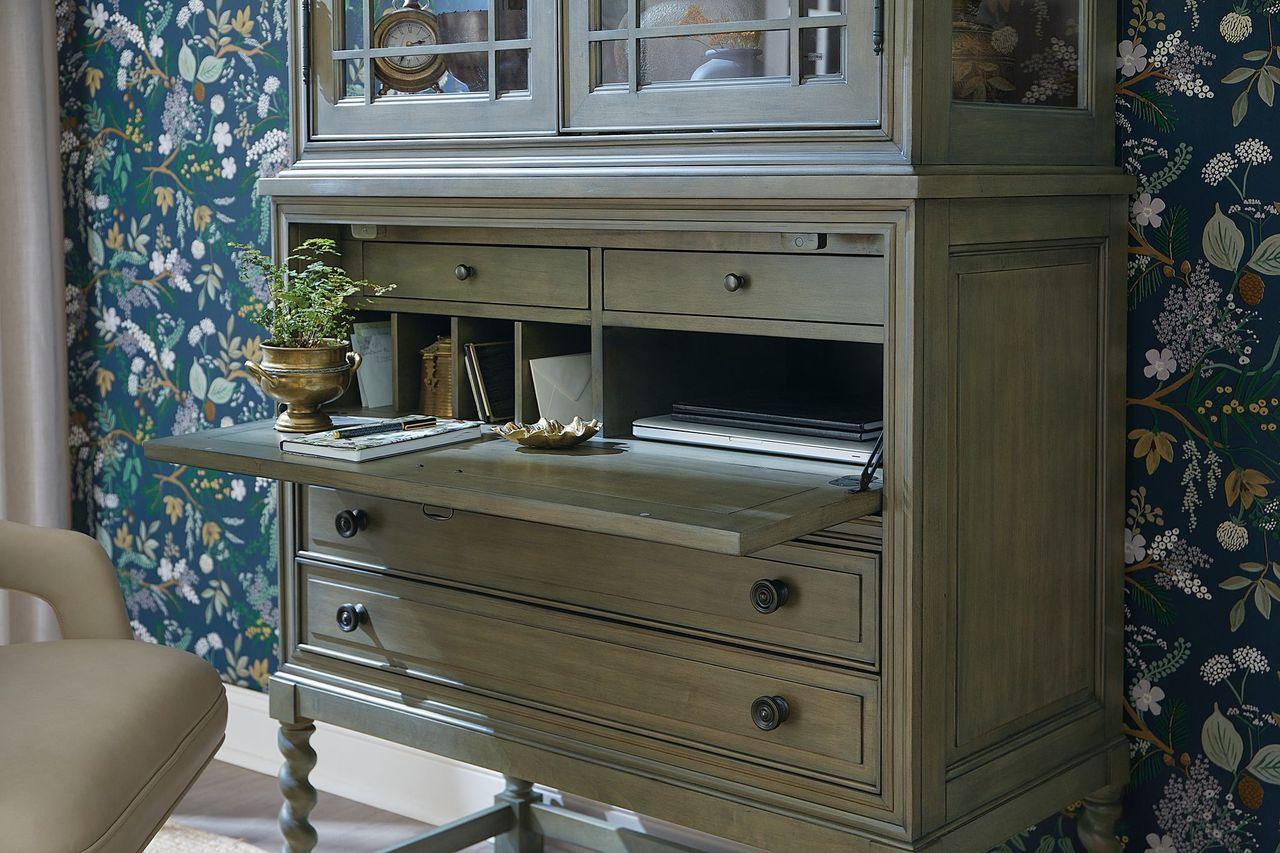
TEMPE, Ariz. — The U.S. economy will continue to softly expand for the rest of 2024, say the nation’s purchasing and supply executives in the Spring 2024 Semiannual Economic Forecast. Expectations for the remainder of 2024 are similar to those expressed in December 2023, despite continued inflation concerns and geopolitical uncertainty.
These projections are part of the forecast issued by the Institute for Supply Management (ISM) Business Survey Committees. The forecast was presented today by Timothy R. Fiore, CPSM, C.P.M., Chair of the ISM Manufacturing Business Survey Committee, and Anthony S. Nieves, CPSM, C.P.M., A.P.P., CFPM, Chair of the ISM Services Business Survey Committee.
According to the report, the Furniture & Related Products category was one of twelve of the 18 industries to report projected revenue increases for the rest of 2024.
In addition, in 2024, the category is:
- one of 12 industries expecting production capacity increases for 2024,
- one of 10 industries expecting capital expenditure increases,
- one of 17 manufacturing industries reporting an increase in prices paid for the first part of 2024, and one of 15 industries expecting price increases for all of 2024,
- and, is one of 12 manufacturing industries expecting increases in revenue in 2024.
The Wood Products category is mentioned only once in the report as one of 10 industries reporting operating capacity levels above the average rate of 82.8 percent.
Here is a truncated version of the ISM report released May 15. For a complete report or more information, visit the Institute of Supply Management. The full text version of each monthly report is posted on www.ismrob.org on the first and third business days of every month after 10:00 a.m. (ET).
Manufacturing Summary
Revenue for 2024 is expected to increase, on average, by 2.1 percent. This is 3.5 percentage points lower than the December 2023 forecast of 5.6 percent, and 1.2 percentage points higher than the 0.9-percentage point year-over-year increase reported for 2023. Forty-four percent of respondents say that revenues for 2024 will increase, on average, 8.6 percent compared to 2023. Fourteen percent say revenues will decrease (12.3 percent, on average), and 42 percent indicate no change. With an operating rate of 82.8 percent and projected increases in capital expenditures (1 percent), prices paid for raw materials (1.9 percent) and employment (0.3 percent) by the end of 2024, the manufacturing sector continues its comeback from the turmoil that began in 2020. “With 12 manufacturing industries expecting revenue growth in 2024 and nine industries expecting employment growth in 2024, panelists forecast that recovery will continue the rest of the year, albeit somewhat softer than originally expected. Sentiment in each industry was generally consistent with performance reports in the April 2024 Manufacturing ISM Report On Business, as well as the fall Semiannual Economic Forecast conducted in December,” says Fiore.
Twelve of 18 industries report projected revenue increases for the rest of 2024, listed in order: Apparel, Leather & Allied Products; Food, Beverage & Tobacco Products; Transportation Equipment; Computer & Electronic Products; Chemical Products; Nonmetallic Mineral Products; Primary Metals; Textile Mills; Furniture & Related Products; Fabricated Metal Products; Electrical Equipment, Appliances & Components; and Paper Products.
Services Summary
Respondents expect a 2.9-percent net increase in overall revenues, which is 4 percentage points lower than the 6.9-percent increase forecast in December 2023. Thirty-six percent of respondents say that revenues for 2024 will increase, on average, 10.3 percent compared to 2023. Meanwhile, 10 percent expect their revenues to decrease (7.5 percent, on average), and 54 percent indicate no change. “The services sector will continue to grow for the rest of 2024. Services companies are currently operating at 88.6 percent of normal capacity. Supply managers indicate that prices are expected to increase 3.2 percent over the year, reflecting increasing inflation. Employment is projected to increase 0.8 percent. Thirteen industries forecast increased revenues, down from the 16 industries that predicted increases in December 2023,” says Nieves.
Thirteen of 18 industries expect revenue increases in 2024, listed in order: Retail Trade; Mining; Transportation & Warehousing; Other Services; Management of Companies & Support Services; Accommodation & Food Services; Professional, Scientific & Technical Services; Construction; Wholesale Trade; Public Administration; Utilities; Information; and Finance & Insurance.
OPERATING RATE
Manufacturing
Purchasing and supply executives report that their companies are operating, on average, at 82.8 percent of normal capacity, 0.2 percentage point lower than the figure reported in December 2023. The 10 industries reporting operating capacity levels above the average rate of 82.8 percent — listed in order — are: Paper Products; Textile Mills; Petroleum & Coal Products; Transportation Equipment; Computer & Electronic Products; Wood Products; Machinery; Primary Metals; Food, Beverage & Tobacco Products; and Fabricated Metal Products.
Services
Organizations are operating, on average, at 88.6 percent of normal capacity, according to Business Survey Committee respondents. This is 2.1 percentage points higher compared to December 2023. The eight industries operating at capacity levels above the average rate of 88.6 percent — listed in order — are: Educational Services; Other Services; Finance & Insurance; Retail Trade; Utilities; Agriculture, Forestry, Fishing & Hunting; Construction; and Public Administration.
Manufacturing
Production capacity is expected to increase 2.4 percent in 2024; in December, panelists reported an increase of 0.7 percentage point for 2023 and projected an increase of 7.8 percent this year. Thirty percent of respondents expect capacity increases of, on average, 12.6 percent; 7 percent expect decreases of, on average, 19.7 percent; and 62 percent expect no change. The 12 industries expecting production capacity increases for 2024 — listed in order — are: Nonmetallic Mineral Products; Furniture & Related Products; Computer & Electronic Products; Food, Beverage & Tobacco Products; Fabricated Metal Products; Primary Metals; Chemical Products; Plastics & Rubber Products; Petroleum & Coal Products; Transportation Equipment; Electrical Equipment, Appliances & Components; and Paper Products.
Services
The capacity to produce products or provide services in the services sector is expected to increase 2.6 percent in 2024. This compares to an increase of 3.9 percent reported for 2023 and a December projection of a 4.1-percent increase for this year. Sixteen percent of services respondents expect their capacity for 2024 to increase, on average, 17.6 percent, and 2 percent foresee capacity decreasing, on average, 11.2 percent. Eighty-two percent expect no change in capacity. The 14 industries expecting production capacity increases for 2024 — listed in order — are: Retail Trade; Mining; Professional, Scientific & Technical Services; Construction; Transportation & Warehousing; Arts, Entertainment & Recreation; Accommodation & Food Services; Wholesale Trade; Information; Management of Companies & Support Services; Public Administration; Health Care & Social Assistance; Utilities; and Finance & Insurance.
PREDICTED CAPITAL EXPENDITURES — 2024 vs. 2023
Manufacturing
Survey respondents expect a 1-percent increase in capital expenditures in 2024, much lower than the 11.9 percent increase forecast by the panel in December. Twenty-four percent of respondents predict increased (on average, 19.8 percent) capital expenditures in 2024, 14 percent said their capital spending would decrease (on average, 26.2 percent), and 62 percent expect no change. The 10 industries expecting capital expenditure increases for 2024 — listed in order — are: Food, Beverage & Tobacco Products; Furniture & Related Products; Nonmetallic Mineral Products; Primary Metals; Fabricated Metal Products; Petroleum & Coal Products; Chemical Products; Paper Products; Transportation Equipment; and Machinery.
Services
This year, services purchasing and supply executives expect capital expenditures to increase 1.4 percent compared to 2023. The 25 percent of respondents expecting to spend more predict an average increase of 16 percent, 12 percent anticipate an average decrease of 20.8 percent, and 63 percent expect no change in capital expenditures in 2024. The 10 industries expecting an increase in capital expenditures — listed in order — are: Public Administration; Utilities; Retail Trade; Accommodation & Food Services; Mining; Transportation & Warehousing; Professional, Scientific & Technical Services; Educational Services; Construction; and Finance & Insurance.
PRICES — Changes Between End of 2023 and May 2024
Manufacturing
In the December forecast, respondents predicted an increase of 3.2 percent in prices paid during the first four months of 2024; they now report prices increased by 1.6 percent. The 45 percent who say their prices are higher now than at the end of 2023 report an average increase of 5.8 percent, while 17 percent reported lower prices (by 6 percent, on average). The remaining 39 percent indicated no change for the period. Seventeen manufacturing industries reported an increase in prices paid for the first part of 2024, listed in order: Textile Mills; Printing & Related Support Activities; Apparel, Leather & Allied Products; Plastics & Rubber Products; Nonmetallic Mineral Products; Primary Metals; Paper Products; Chemical Products; Computer & Electronic Products; Machinery; Miscellaneous Manufacturing; Fabricated Metal Products; Petroleum & Coal Products; Electrical Equipment, Appliances & Components; Transportation Equipment; Furniture & Related Products; and Food, Beverage & Tobacco Products.
Services
Services respondents report that purchases during the first four months of this year cost an average of 2.3 percent more than at the end of 2023. This is 1.4 percentage points less than the 3.7-percent increase predicted in December. Forty-six percent of services respondents report that prices increased, on average, 6.7 percent; 11 percent report price decreases of, on average, 7.2 percent; and 43 percent indicate no change. Fourteen of 18 industries reported an increase in prices paid in the first part of 2024, listed in order: Public Administration; Management of Companies & Support Services; Utilities; Retail Trade; Professional, Scientific & Technical Services; Transportation & Warehousing; Construction; Educational Services; Finance & Insurance; Health Care & Social Assistance; Wholesale Trade; Arts, Entertainment & Recreation; Other Services; and Information.
PRICES — Predicted Changes Between End of 2023 and End of 2024
Manufacturing
Survey respondents expect a year-over-year, net-average prices increase of 1.9 percent for 2024. With respondents reporting price increases of 1.6 percent through April 2024, prices are projected to increase slightly for the rest of the year. Forty-seven percent of respondents project prices to increase, on average, 6.1 percent for the full year, 20 percent anticipate a decrease (5.2 percent, on average), and 33 percent expect no change. The 15 industries expect price increases for all of 2024, listed in order are: Textile Mills; Apparel, Leather & Allied Products; Primary Metals; Plastics & Rubber Products; Nonmetallic Mineral Products; Chemical Products; Paper Products; Furniture & Related Products; Fabricated Metal Products; Transportation Equipment; Miscellaneous Manufacturing; Petroleum & Coal Products; Computer & Electronic Products; Electrical Equipment, Appliances & Components; and Machinery.
Services
This year, services respondents expect prices to increase, on average, 3.2 percent compared to the end of 2023. With respondents reporting an increase of 2.3 percent through April 2024, prices are projected to increase over the rest of the year. Forty-eight of respondents anticipate increases of, on average, 7.2 percent; 7 percent expect decreases of, on average, 5 percent; and 45 percent do not expect prices to change. Fifteen of 18 industries project price increases for all of 2024, listed in order: Public Administration; Retail Trade; Arts, Entertainment & Recreation; Utilities; Wholesale Trade; Management of Companies & Support Services; Construction; Health Care & Social Assistance; Professional, Scientific & Technical Services; Educational Services; Finance & Insurance; Transportation & Warehousing; Accommodation & Food Services; Information; and Other Services.
EMPLOYMENT
Employment — Predicted Changes Between End of 2023 and End of 2024
Manufacturing
ISM’s Manufacturing Business Survey Committee respondents forecast that sector employment in 2024 will increase 0.3 percentage point year over year. Twenty-three percent of respondents expect employment to be, on average, 7.4 percent higher; 15 percent predict employment to decrease, on average, 8.7 percent; and 62 percent expect employment levels to be unchanged. The nine industries projecting employment growth during 2024 — listed in order — are: Nonmetallic Mineral Products; Food, Beverage & Tobacco Products; Primary Metals; Plastics & Rubber Products; Petroleum & Coal Products; Fabricated Metal Products; Textile Mills; Computer & Electronic Products; and Chemical Products.
Services
Sector employment will increase 0.8 percent in 2024, according to the forecast of ISM’s Services Business Survey Committee respondents. For the remaining months of the year, 25 percent expect employment to increase, on average, 5.2 percent; 8 percent anticipate employment to decrease, on average, 7 percent; and 67 percent expect no change in employment levels. The 13 industries anticipating increases in employment — listed in order — are: Other Services; Retail Trade; Accommodation & Food Services; Mining; Arts, Entertainment & Recreation; Construction; Transportation & Warehousing; Utilities; Public Administration; Health Care & Social Assistance; Wholesale Trade; Real Estate, Rental & Leasing; and Professional, Scientific & Technical Services.
BUSINESS REVENUES
Business Revenues Comparison — 2024 vs. 2023
Manufacturing
Increased revenues are expected this year, as purchasing and supply management executives predict an overall net increase of 2.1 percent compared to 2023. This is 3.5 percentage points lower than the 5.6-percent increase forecast in December, and 1.2 percentage points higher than the 0.9-percentage point year-over-year increase reported for 2023. Forty-four percent of respondents say that revenues for 2024 will increase, on average, 8.6 percent; 14 percent say their revenues will decrease, on average, 12.3 percent; and 42 percent forecast no change. The 12 manufacturing industries expecting increases in revenue in 2024 — listed in order — are: Apparel, Leather & Allied Products; Food, Beverage & Tobacco Products; Transportation Equipment; Computer & Electronic Products; Chemical Products; Nonmetallic Mineral Products; Primary Metals; Textile Mills; Furniture & Related Products; Fabricated Metal Products; Electrical Equipment, Appliances & Components; and Paper Products.
Services
This year, services purchasing and supply management executives predict a net increase of 2.9 percent in sector business revenue compared to 2023. This is 4 percentage points lower than the 6.9-percent increase forecast in December, and 1.3 percentage points lower than the 4.2-percent increase reported for 2023. Thirty-six percent of respondents indicate revenues for 2024 will increase, on average, 10.3 percent; 10 percent say their revenues will decrease, on average, 7.5 percent; and 54 percent expect no change. Thirteen of 18 services industries project revenue increases in 2024, listed in order: Retail Trade; Mining; Transportation & Warehousing; Other Services; Management of Companies & Support Services; Accommodation & Food Services; Professional, Scientific & Technical Services; Construction; Wholesale Trade; Public Administration; Utilities; Information; and Finance & Insurance.
May 19, 2024
Tosoh to Increase Prices for Millionate MDI Grades
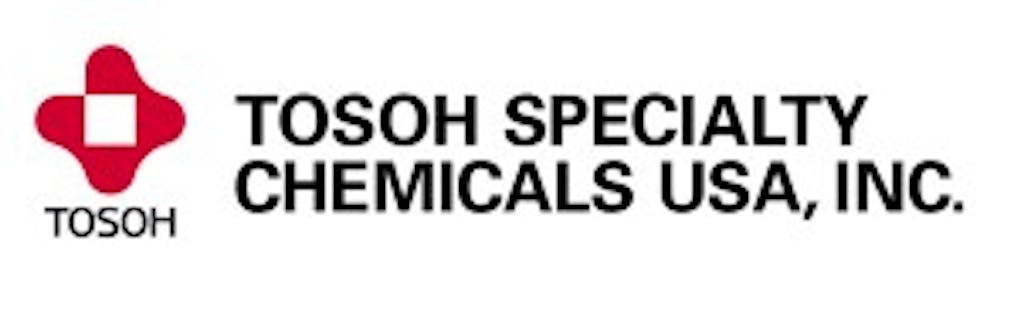
Tosoh Specialty Chemicals USA, Inc. is increasing its prices for Millionate MDI Grades in North America. Effective with deliveries on or after June 1, 2024, or as contract terms allow, TSCU will increase the prices of Millionate MDI grades by $0.25/kg.
Millionate MDI is widely used in the production of rigid, semi-rigid, and integral skin foams, as well as coatings, adhesives, and elastomers.
TOSOH CORPORATION
Tosoh Corporation is the parent company of a Japanese chemical and specialty products and materials group that comprises over 100 companies worldwide and a multiethnic workforce of more than 12,000 people.
The parent company was established in 1935 and is listed on the First Section of the Tokyo Stock Exchange. In the 80 years that we have been in business, we have built balanced product lines of commodity chemicals for industry and of specialty products and materials for high technology and niche markets.
Tosoh’s principal markets include the chemical and petrochemical, construction, automotive, consumer electronics, information technology, bioscience, and environmental markets.
May 19, 2024
Chemical Data Reporting under the Toxic Substances Control Act
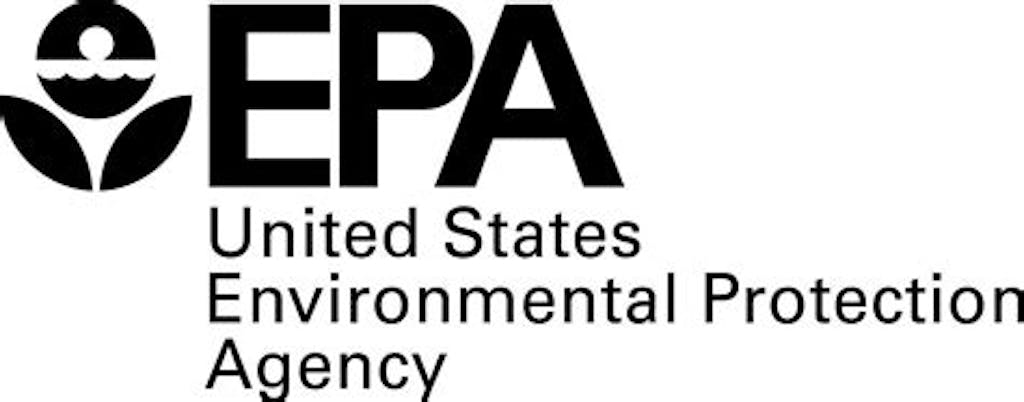
- The 2024 CDR Reporting Period is Opening Soon The 2024 CDR submission period begins June 1, 2024, and runs through September 20, 2024. Companies are required to report data electronically using EPA’s Central Data Exchange (CDX) systemand the e-CDRweb reporting tool which will be available starting June 1.
- Guidance on submitting information to the CDR database for 2024.
- CDR GuideMe guidance database
- 2020 CDR National Review EPA published a review summarizing the 2020 CDR site locations, production volumes, industrial uses, and commercial/consumer uses, as well as, data trends from the last three reporting cycles.
- The 2024 CDR Reporting Period is Opening Soon The 2024 CDR submission period begins June 1, 2024, and runs through September 20, 2024. Companies are required to report data electronically using EPA’s Central Data Exchange (CDX) systemand the e-CDRweb reporting tool which will be available starting June 1.
- Guidance on submitting information to the CDR database for 2024.
- CDR GuideMe guidance database
- 2020 CDR National Review EPA published a review summarizing the 2020 CDR site locations, production volumes, industrial uses, and commercial/consumer uses, as well as, data trends from the last three reporting cycles.
The Chemical Data Reporting (CDR) rule, under the Toxic Substances Control Act (TSCA), requires manufacturers (including importers) to provide EPA with information on the production and use of chemicals in commerce.
Basic Information
2020 National Review
CDR Data
Regulatory Overview
- CDR Petitions
- Proposed TSCA Data Reporting Rule
- Legislative and regulatory authority
- 40 CFR Part 711, (TSCA CDR Requirements)