Polyurethane Foam Association Sets Technical Presentations For November 2017 Meeting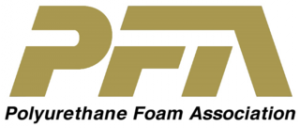
LOUDON, TN (September 26, 2017)— The Polyurethane Foam Association has finalized its slate of presentations for its fall Technical Program, to be held in conjunction with its annual Fall meeting, October 31-November 2, at the Wyndham Bayside Hotel in San Diego, CA.
Following are abstracts for the presentations to be made during the Technical Program on November 2:
Introducing SlabProcessing and SlabExpert Digital Tools
Covestro LLC
Presenter: Stephen Hoskins
This paper introduces Covestro i4ptO™ 24/7 online digital services to support flexible polyurethane foam R&D and manufacturing initiatives. Under the i4ptO™ “umbrella,” SlabExpert software allows slabstock foamers to more efficiently and effectively formulate using Covestro raw materials, while SlabProcessing provides a custom-service that helps slab manufacturers more effectively collect, monitor and compare production data and processes. Covestro digital tools serve as self-technical service improvement opportunities that interpret thousands of data points to provide new, precise perspectives to the development and processing of slab foam. Through the creation of cloud-based, low-cost, flexible, and scalable products, we are excited to introduce these tools to support the slabstock foam industry.
Flammability Standards for Upholstered Furnishings and Vehicles: Past, Present, and Future
Fire Science and Technology Inc.
Presenter: Vytenis Babrauska
Since the 1970s, flammability standards for furnishings and vehicle interiors have led to use of flame retardants (FRs) in FPF. Research continues to demonstrate exposures and health risks from the use of FRs. Despite recent progress in California, voluntary standards organizations (VSOs) continue to work towards new flammability requirements for furniture; and federal motor vehicle flammability requirements remain and are outdated. Europe currently does not have a unified flammability requirement for residential upholstered furniture; however, a petition was filed in 2016 asking the E.U. government to consider a mandatory smolder standard for European furniture based on TB117-2013. This presentation will demonstrate that the most effective way to reduce harm from flame retardants is to improve flammability standards. To enhance fire safety, benign strategies should be considered that have a proven track record of success and do not lead to widespread exposures to hazardous chemicals. These include improvements in smoke alarm technology, wider introduction of automatic fire sprinklers, and enhanced public education efforts.
Vertifoam Variable Pressure Foaming, VPF-V: Full-scale Production Insights
OPUS Technical Ltd
Presenter: Brian Blackwell
The Vertifoam Variable Pressure Foaming Machine, VPF-V, is now in full commercial production. This paper gives insights into the operation of the VPF-V process and shows how the VPF-V equipment and process have been developed and refined to produce highly successful new foam that has opened up new profitable markets for the PU foam industry. The paper explains how a number of both formulation and equipment developments have given improved cell structure and bun yields. It explains how a unique high pressure technology has been applied to the process giving multiple advantages, and how a brand new technique was employed to allow extended runs (over 5 hours) of highly reactive formulations without the problems normally associated with build-up. Formulation savings will be explained, as well as the efficiency of peeling large diameter, near perfect round buns, to produce a new range of foams that can outperform polyester fiber in both cost and performance for bedding and furniture applications.
Case Study in TDI Detection Using IMS Instruments in Foam Plants
Bruker Detection Corporation
Presenter: Frank Thibodeau
Ion Mobility Spectrometry (IMS) is a scientific technique of measuring ions across a uniform electric field. It is based on the principle that when different charged molecules (ions) are accelerated through an electric field (with a “drift flow” of gas slightly opposing them); they will travel at different speeds and reach a detector at different times. The advantages of IMS instruments are: designed in relatively small packages, fairly inexpensive, rugged, extremely fast and extremely sensitive. The effectiveness of the IMS technology has been assessed in numerous foam plants under field conditions. TDI was monitored in foam plants which produced automotive and slab products. A handheld IMS instrument surveyed in and around production lines, hot & cold foam, storage tanks, transfer lines, and transfer operations. The IMS instrument was programmed with a TDI library fixed to detect and alarm at or below 1 ppb. Spectra were also collected at various locations at all foam plants for more detailed post analysis. Findings, lessons learned and conclusions will be discussed in the technical paper and presentation.
Antimicrobial Treatment of Polyurethane Foams
Lonza Microbial Control
Presenter: Tom Robitaille
The use of antimicrobials in polyurethane foam applications continues to grow as the number of antimicrobial options continue to shrink. End-users and component manufacturers are specifying very rigorous performance characteristics. Identifying the right antimicrobial product can be a daunting task. There are many factors to consider when identifying the best antimicrobial product and loading. The EPA only allows certain registered products to be used in specific applications and substrates; these regulations should be understood. Characterization of possible reactivity changes must also be understood as well as the impact on air flow and cell size. Depending on the physical nature of the antimicrobial product to be used, solid dispersion or liquid, and viscosity, processes used to add and pump the antimicrobial into the foam should be reviewed. The intent of this paper will be to educate those that may be considering the addition of an antimicrobial for the first time or maybe considering switching to a different antimicrobial product. This paper can serve as a guide for consideration as you prepare to make the change to an antimicrobially treated polyurethane foam.
Why Is An Ultra-Open-Cell-Window Structure Important For Cooler Sleep In Memory Foam Mattresses?
The Dow Chemical Company
Presenter: Wenbo Xu
Viscoelastic memory foams are widely used as an important material for mattress constructions, due to their pressure relieving capability. A characteristic of memory foam mattresses early on has been that they can “sleep hot” as described by a mattress OEM in patent literature. A new ultra-high air flow memory foam technology was introduced in 2016. Simulation and materials testing capabilities at Dow Chemical were used to evaluate the various materials and their contribution to cooling effects: gas convection, gas/solid conduction, and gas diffusivity. The simulations are multiphysical in nature, taking into account thermal & mass transfer, and feedback loop from human body via the ASHRAE Human Comfort model. The same simulation capabilities are able to support the development of new generation of foam material that improve on thermal comfort.
Registration for the meeting is open, with a discounted room rate cutoff date of October 9. To register, visit www.pfa.org.
Because the program includes at least six technical papers, the presentations will be scored to compete for a $500 Technical Excellence Award provided by the Herman Stone Family Endowment.